Plasma Cutting Line
Cebora manufactures a range of plasma cutting power sources devoted to the automated cutting, either for High Definition cutting (HQC = High Quality Cut) or for standard one.
Power sources, torches and consumables are the result of Cebora's multi-year research in this sector, carried out also in cooperation with the University of Bologna. Such research has brought to the creation of particularly reliable and performing power sources, completed by torches that assure optimal cutting speed and thickness.
Standard Definition Inverter Plasma Cutters
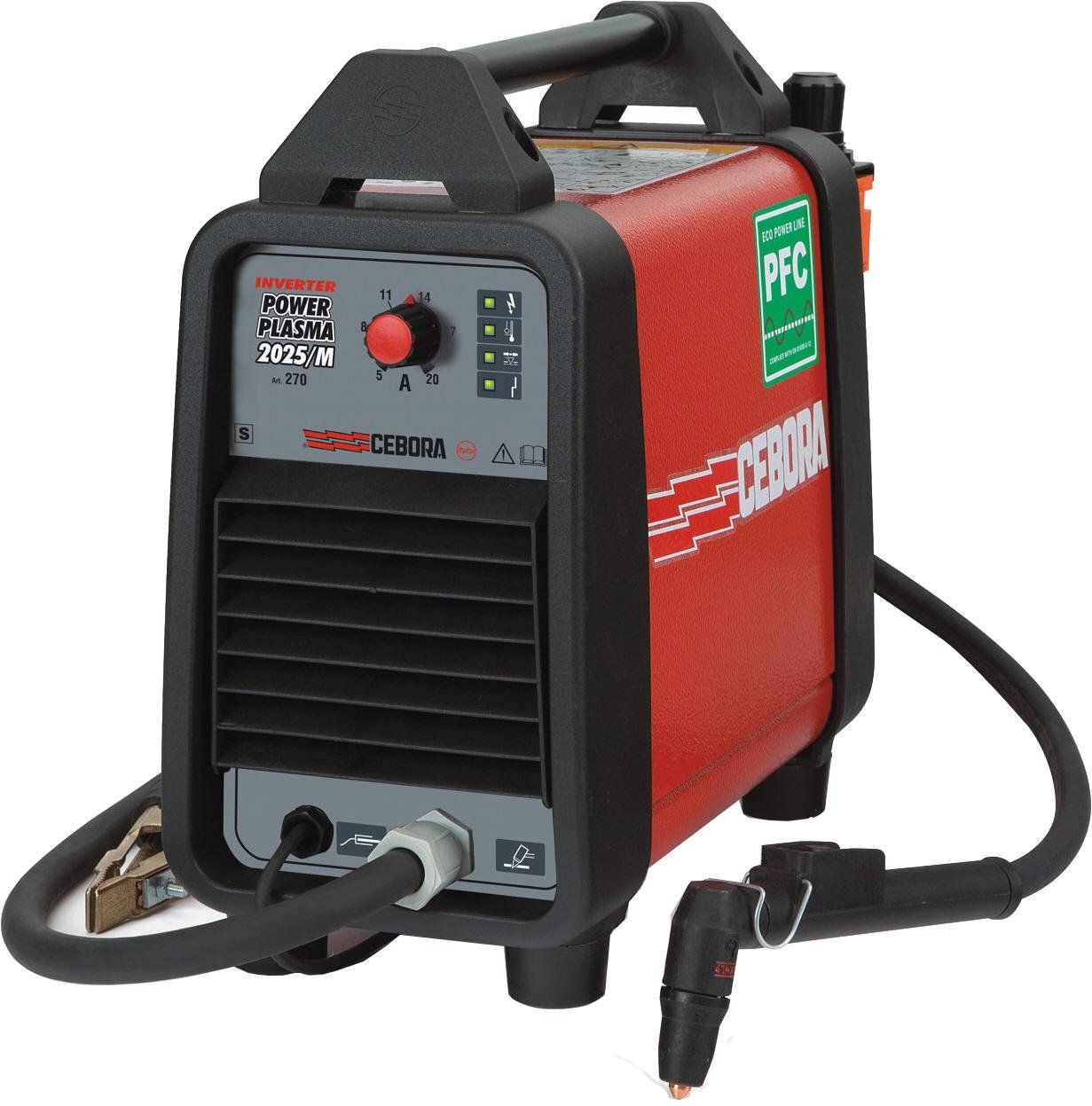
Power Plasma 2025/M - Plasma Inverter (Art 270)
POWER PLASMA 2025/M
was reated to meet the need of working with an easy to handle, easy to use power source with minimal system
requirements (2,3 KVA at the maximum power) yet able to ensure excellent quality cutting on all metals.
POWER PLASMA 2025/M weights just 9,4 kg including the torch, and requires single-phase power supply; it works with compressed air provided at a pressure of 3.5 bar, with an air flow of just 55 l/min (and may thus be powered by a 25-l compressor).
- Pilot arc “on air” operating mode, which makes it possible to work even on painted or coated metals.
- Equipped with a 4 m new Cebora CP41C plasma cutting torch, with “on air” ignition without high frequency.
- High electromagnetic compatibility, per IEC 60974-10, allowing the power source to be used in the vicinity of electronic equipment (such as computers, PLC, etc.).
- Explosion-proof protection of the air reducer unit.
The compliance with EN 61000-3-12
brings substantial energy saving and a wide supply voltage tolerance (+15% / -20%).
The power source can also be powered by motor-driven generators of adequate power (min. 4KVA).
Power Plasma 3035/M Plasma Inverter (Art 279)
POWER PLASMA 3035/M
is an easy to handle, easy to use power source with minimal system requirements, able to ensure excellent quality cutting on all metals, including the new high-strength steels.
POWER PLASMA 3035/M weights just 13 kg including the torch, and requires single-phase power supply; it works with compressed air or nitrogen (for high-quality cutting), provided at a pressure of 3.5 bar, with an air flow of just 60 l/min (and may thus be powered by a 25-l compressor).
The recommended thickness, for the best cutting quality and productivity, is 8 mm; the maximum thickness is 12 mm and the severance thickness is 15 mm.
- Automatic voltage change (115/230 V +15% / -20%).
- Pilot arc operating mode, which makes it possible to work even on painted or coated metals.
- Pilot self-restart, selectable from the panel, to interrupt and automatically reset the arc when cutting screens and grids, increasing operator productivity.
- Nozzle holder protection, as required by standards IEC 60974-7, which eliminates the risk to the operator of direct accidental contact with the gas nozzle.
- High voltage arc striking with high frequency, to ensure reliable lighting of the pilot arc and reduced disturbances.
- High electromagnetic compatibility, per EN50199, allowing the power source to be used in the vicinity of electronic equipment (such as computers, PLC, etc.).
- Explosion-proof protection of the air reducer unit.
The power source is particularly suitable for cutting the overlapped sheets that are commonly used in the car bodies
The compliance with EN 61000-3-12 brings substantial energy saving and a wide supply voltage tolerance (+15% / -20%).
The power source can also be powered by motor-driven generators of adequate power (min. 6KVA).
Cutting Speed Diagram
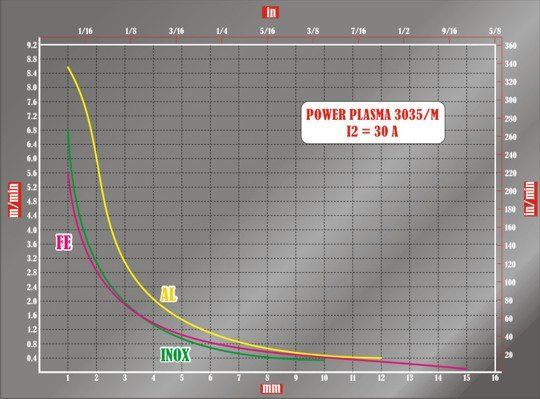
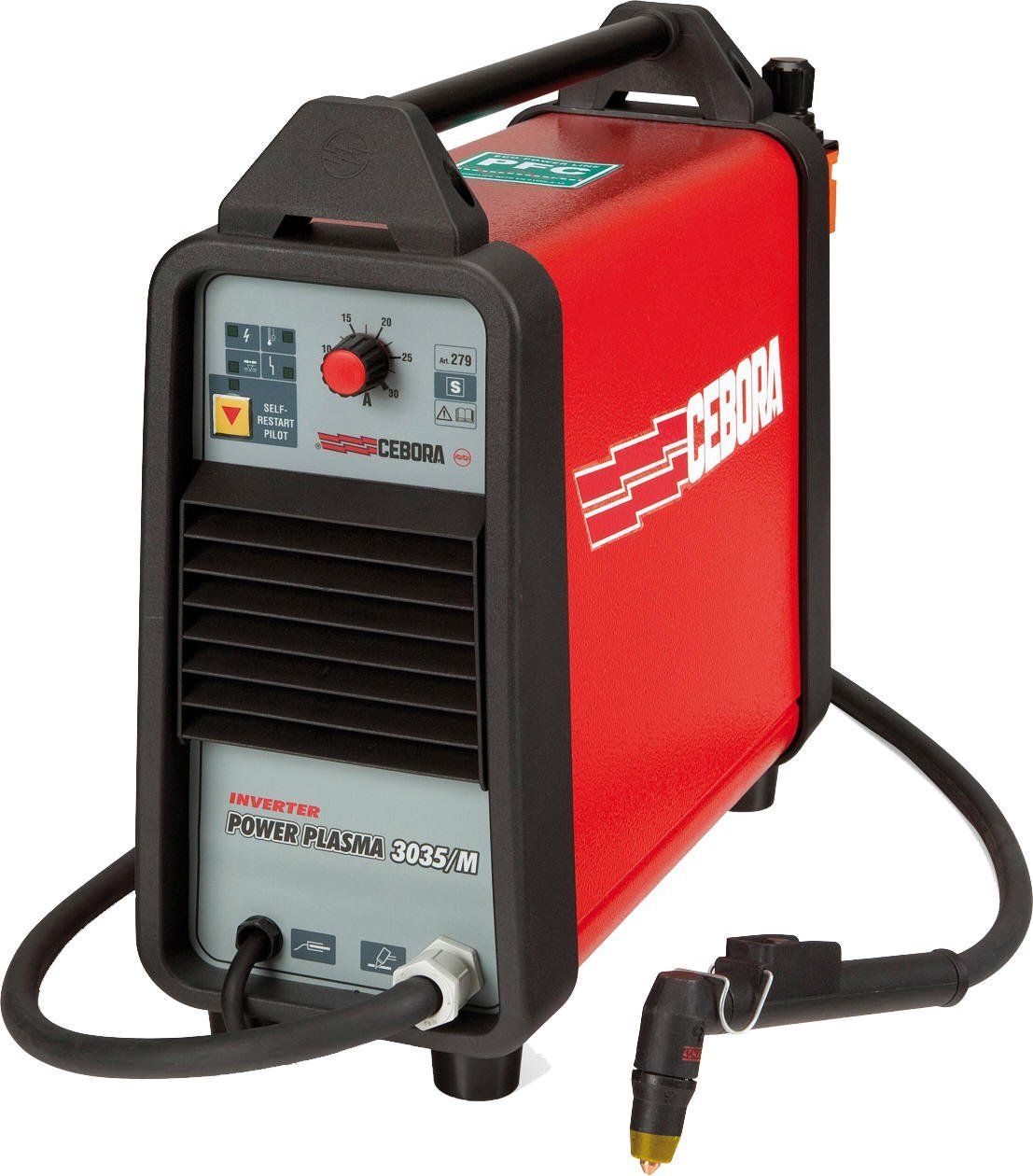
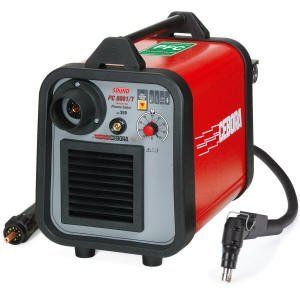
Plasma Sound PC 6061/T (Art. 359)
The POWER PLASMA 6061/T
is a three-phase power source for plasma cutting of metals.
Thanks to the new manual air cooled CP 101 MAR torch,the recommended thickness, for the best cutting quality and productivity, is 20 mm; the maximum thickness is 25 mm and the severance thickness is 30 mm. Its reduced size and weight make the PLASMA SOUND PC 6061/T ideal for on-site work and manual production of medium intensity (60A@60%) and for small automatic production applications, thanks to the cutting speeds and to the high continuous duty cycle (50A@100%).
- Automatic voltage change (208V-220V-230V-400V-440V +/-10%)
- Automatic detection of phase presence (both upon start-up and during operation), to avoid damaging the machine in case the phase is accidentally missing.
- “Post-gas” function which, by cooling the torch after arc shut-off, reduces stress on the components and extends the life-span of consumables.
- Pilot arc operating mode, which makes it possible to work even on painted or coated metals.
- Full-bridge design which allows lower open-circuit voltages.
- Pilot self-restart, selectable from the panel, to interrupt and automatically reset the arc when cutting nets and grids, increasing operator productivity.
- High frequency and high voltage arc striking, which ensures reliable striking of the pilot arc and reduces disturbances.
- High electromagnetic compatibility, per EN50199, allowing the power source to be used in the vicinity of electronic equipment (such as computers, PLC, etc.).
- Central torch adapter with safety protection, to avoid accidental contact with the power parts.
- Explosion-proof protection of the air reducer unit.
- Standard equipped with 6 m CP 101 MAR torch.
Complies with EN 61000-3-12.
The power source can also be powered by motor-driven generators.
Cutting Speed Diagram
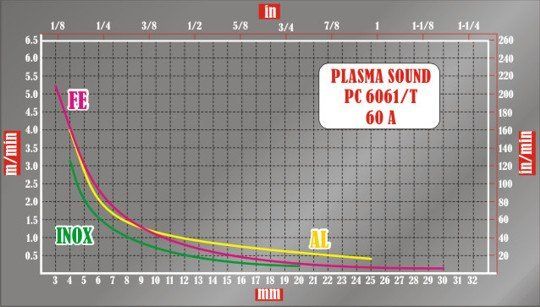
Plasma Sound PC 10051/T (Art. 361)
The PLASMA SOUND 10051/T
three-phase power source for plasma cutting of metals represents the upward evolution of the 6061/T.
Thanks to the new manual aircooled CP 161 torch, the recommended thickness, for the best cutting quality and productivity, is 30 mm; the maximum thickness is 35 mm and the severance thickness is 40 mm. The high continuous (85A@100%) and discontinuous (95A@60%) duty cycle and the cutting speed make the PLASMA SOUND PC10051/T ideal for automatic production applications, as well as for manual productions of average size.
- Automatic detection of phase presence (both upon start-up and during operation), to avoid damaging the machine in case the phase is accidentally missing.
- Pilot arc operating mode, which makes it possible to work even on painted or coated metals.
- “Post-gas” function which, by cooling the torch after arc shut-off, reduces stress on the components and extends the life-span of consumables.
- Full-bridge design that allows lower open-circuit voltages
- High electromagnetic compatibility, per EN50199, allowing the power source to be used in the vicinity of electronic equipment (such as computers, PLC, etc).
- High voltage arc striking with high frequency, to ensure reliable lighting of the pilot arc.
- Central torch adapter with safety protection, to avoid accidental contact with the power parts.
- Explosion-proof protection of the air reducer unit.
- “Pilot self-restart” function selectable from the panel, which interrupts and automatically restarts the arc when cutting nets and grids, increasing operator productivity.
- Automatic voltage change between 208/220/230V and between 400/440 V.
- Standard equipped with 6 m CP161 MAR torch
Complies with EN 61000 - 3 - 12
The power source can also be powered by motor-driven generators.
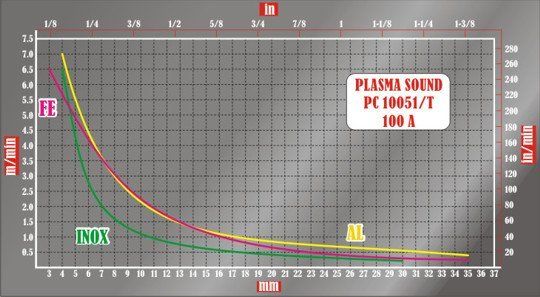
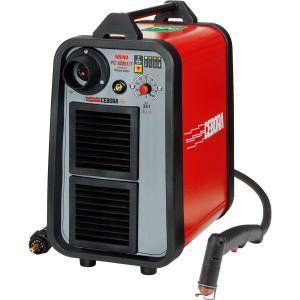
Standard Definition 'Chopper' Plasma Cutters
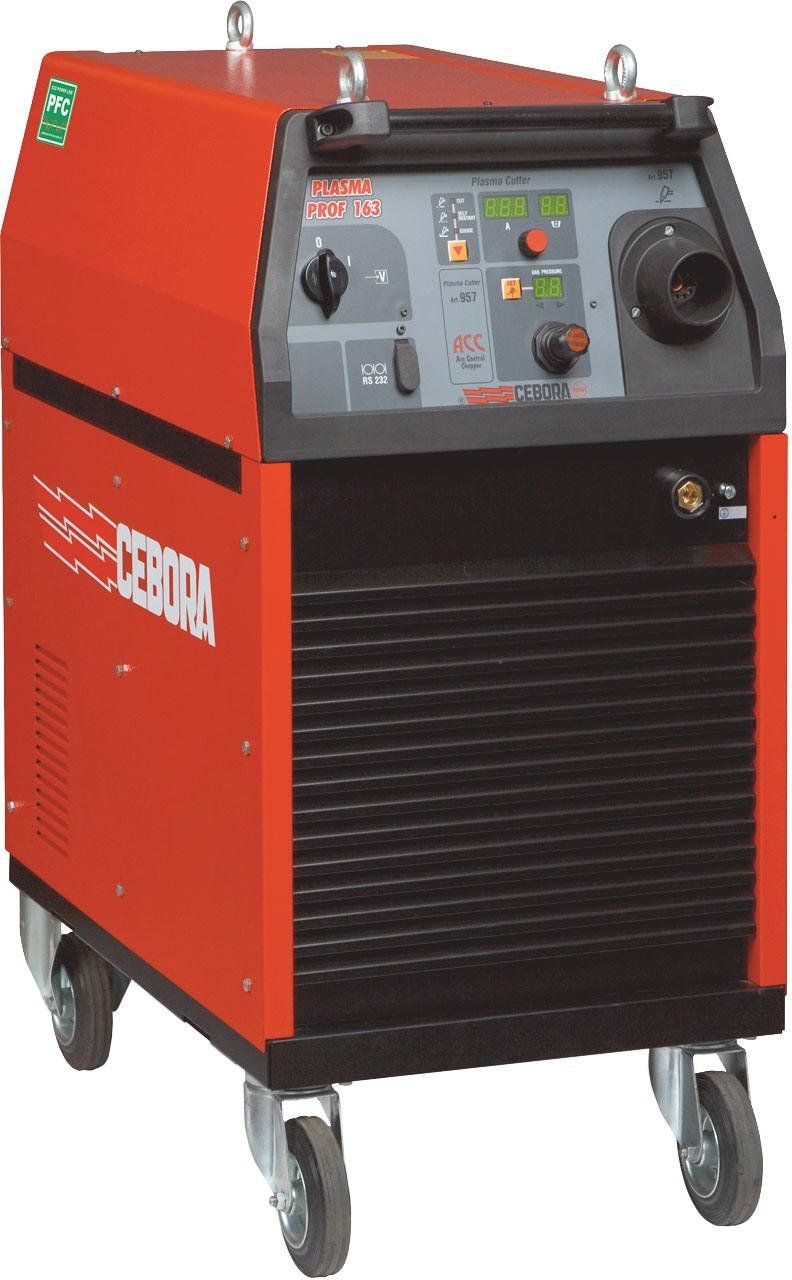
Plasma Prof 163 ACC (Chopper) Art.957
The PLASMA PROF 163 ACC
three-phase “chopper” multi-voltage power source, art. 957, thanks to its remarkable power (160A at 40%) and to the new CP161 torch, assures excellent performances in metal cutting (the recommended thickness, for the best compromise between cutting quality and productivity, is 40 mm; the maximum thickness is 45 mm and the severance thickness is 50 mm. The maximum piercing thickness is 20 mm.
Complies with EN 61000 - 3 - 12
The high continuous (95A at 100%) duty cycle and the cutting speed make the PLASMA PROF 163 ACC ideal for productions of average size.
Main features:
- Continuous monitoring of the supply voltage, detection of abnormal conditions (e.g. missing phase) and safety stop of the power source.
- Air pressure adjustment and test and optimal pressure display, according to the cutting current and to the torch length, on the front panel.
- “Post-gas” function which, by cooling the torch after arc shut-off, reduces stress on the components and extends the life-span of consumables.
- High voltage arc striking with high frequency, to ensure reliable lighting of the pilot arc.
- Reduced electrode-nozzle wear.
- Central torch adapter with safety protection, to avoid accidental contact with the power parts.
- Explosion-proof protection of the air reducer unit.
- Gouging mode that can be selected from the front panel.
- Pilot self-restart function, selectable from the panel, to interrupt and automatically reset the arc when cutting grids.
- Display showing the cutting current and the relevant nozzle diameter to be used.
- RS232 connector on the front panel for updating or customizing the machine software.
- Can be equipped with either 6 or 12 m CP161 torch, for either manual or automated use.
- Ready for use with cutting pantographs by means of analogic interface art. 108 (optional). A remote high frequency unit (art. 481, optional) is also available in order to obtain a maximum total torch cable length of 22 m.
- Automatic recognition of the torch: CP161 MAR / DAR / DAR+HV14.
- Chopper technology and 17 kHz working frequency.
Complies with EN 61000 - 3 - 12
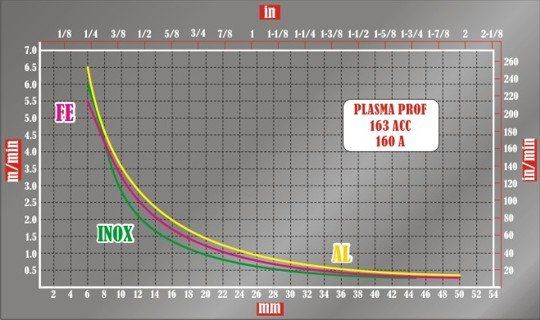
High definition: HQC plasma cutting power sources and torches
Plasma Prof 165 HQC (Art.958)
The Cebora HQC (High Quality Cutting) plasma cutting systems devoted to the automation
were born from our long experience in plasma cutting, joined to the professionalism and theoretical support of sophisticated simulation systems of the prestigious Unit for the Industrial Applications of Plasma of the University of Bologna.
They are complete systems for High Quality Cutting with plasma gases, on all metallic materials, consisting of extremely sophisticated electronic power sources capable to supply, in continuous, 120A, 250A and 420A respectively, thus obtaining cuts on maximum thicknesses of 35, 60 and 80 mm with a quality up to range 2 according to the international reference standard ISO 9013.
Such results have been made possible thanks to the integrated development and to the direct manufacture of each single part of these systems, that also include:
- Semi-automatic Synergic Gas Console (PGC) for an error-proof manual setting of the cutting parameters
- Automatic Gas Console (APGC) for the complete programming of the cutting system from the pantograph / robot CNC, as well as the control and the continuous adjustment of the cutting gas flows
- High Frequency sources for quick and precise ignitions of the electric arc
- Gas Valves Unit for the supply and the exchange between the different gas flows allowing to obtain the best quality since the cut start, even on the thinner materials.
The real heart of these systems are the Cebora CP251G and CP450G (bevel) torches, with their relevant consumables (for which Cebora already deposited several patents), the cutting performances and service life of which represent the current state of the art. A particular care was devoted to the operating inexpensiveness, thus assuring an extremely reduced gas consumption in comparison to the competition, that makes the investment, in the Cebora HQC cutting systems, quickly amortizable.
The progressive increase of the demand for 3D cutting systems, implemented using either pantographs equipped with bevel cutting units or anthropomorphous robots, brought Cebora to develop a complete family of bevel torches with relevant consumables, that is the CP450G series, just devoted to the 3D cut, either for pantograph or for robot. The CP450G bevel torches are distinguished by dimensions and technical solutions expressly designed for these applications and allow space need as well as freedom and integration degrees that these same solutions require.
To the torches have also been added robot interfaces capable to satisfy any interconnection need: from the traditional analogic interfaces to the most modern and sophisticated digital ones, based on the main industrial BUS.
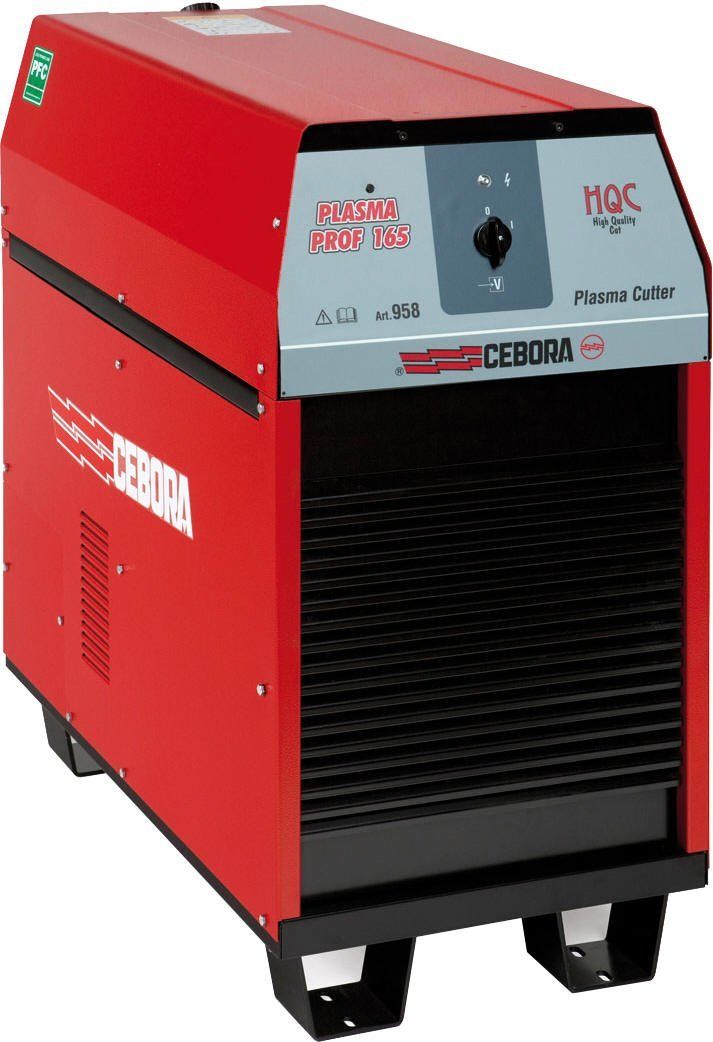
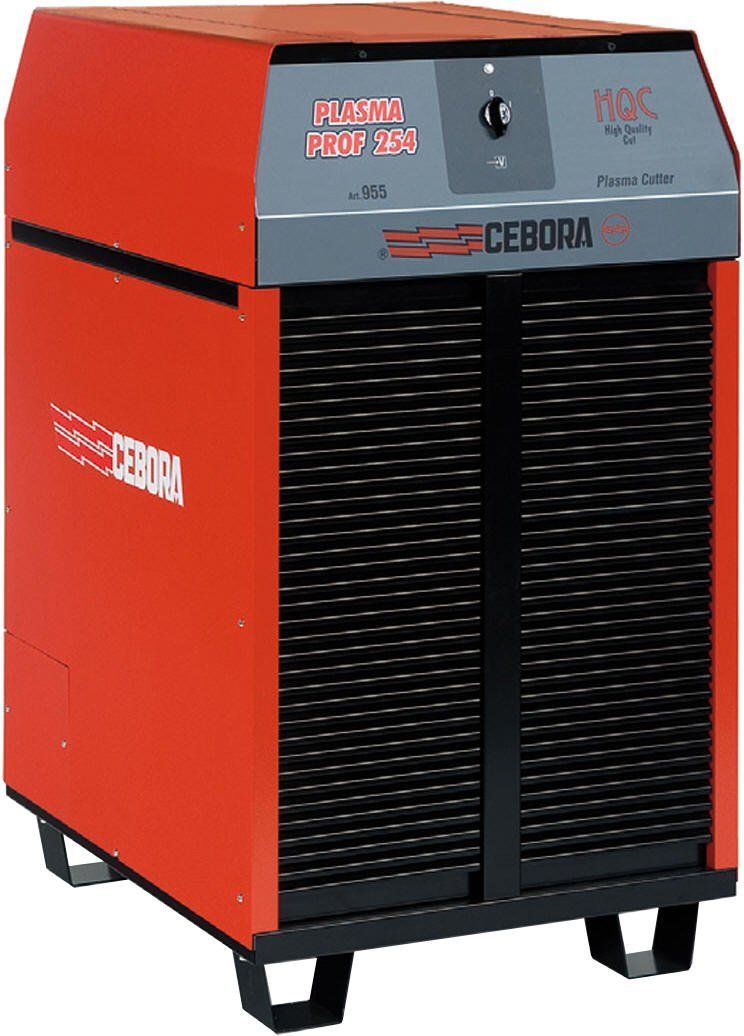
Plasma Prof 254 HQC (Art. 955)
The Cebora HQC (High Quality Cutting) plasma cutting systems devoted to the automation
were born from our long experience in plasma cutting, joined to the professionalism and theoretical support of sophisticated simulation systems of the prestigious Unit for the Industrial Applications of Plasma of the University of Bologna.
They are complete systems for High Quality Cutting with plasma gases, on all metallic materials, consisting of extremely sophisticated electronic power sources capable to supply, in continuous, 120A, 250A and 420A respectively, thus obtaining cuts on maximum thicknesses of 35, 60 and 80 mm with a quality up to range 2 according to the international reference standard ISO 9013.
Such results have been made possible thanks to the integrated development and to the direct manufacture of each single part of these systems, that also include:
- Semi-automatic Synergic Gas Console (PGC) for an error-proof manual setting of the cutting parameters
- Automatic Gas Console (APGC) for the complete programming of the cutting system from the pantograph / robot CNC, as well as the control and the continuous adjustment of the cutting gas flows
- High Frequency sources for quick and precise ignitions of the electric arc
- Gas Valves Unit for the supply and the exchange between the different gas flows allowing to obtain the best quality since the cut start, even on the thinner materials.
The real heart of these systems are the Cebora CP251G and CP450G (bevel) torches, with their relevant consumables (for which Cebora already deposited several patents), the cutting performances and service life of which represent the current state of the art.
A particular care was devoted to the operating inexpensiveness, thus assuring an extremely reduced gas consumption in comparison to the competition, that makes the investment, in the Cebora HQC cutting systems, quickly amortizable.
The progressive increase of the demand for 3D cutting systems, implemented using either pantographs equipped with bevel cutting units or anthropomorphous robots, brought Cebora to develop a complete family of bevel torches with relevant consumables, that is the CP450G series, just devoted to the 3D cut, either for pantograph or for robot. The CP450G bevel torches are distinguished by dimensions and technical solutions expressly designed for these applications and allow space need as well as freedom and integration degrees that these same solutions require.
To the torches have also been added robot interfaces capable to satisfy any interconnection need: from the traditional analogic interfaces to the most modern and sophisticated digital ones, based on the main industrial BUS.
Plasma Prof 420 HQC (Art. 960)
The Cebora HQC (High Quality Cutting) plasma cutting systems devoted to the automation
were born from our long experience in plasma cutting, joined to the professionalism and theoretical support of sophisticated simulation systems of the prestigious Unit for the Industrial Applications of Plasma of the University of Bologna.
They are complete systems for High Quality Cutting with plasma gases, on all metallic materials, consisting of extremely sophisticated electronic power sources capable to supply, in continuous, 120A, 250A and 420A respectively, thus obtaining cuts on maximum thicknesses of 35, 60 and 80 mm with a quality up to range 2 according to the international reference standard ISO 9013.
Such results have been made possible thanks to the integrated development and to the direct manufacture of each single part of these systems, that also include:
- Semi-automatic Synergic Gas Console (PGC) for an error-proof manual setting of the cutting parameters
- Automatic Gas Console (APGC) for the complete programming of the cutting system from the pantograph / robot CNC, as well as the control and the continuous adjustment of the cutting gas flows
- High Frequency sources for quick and precise ignitions of the electric arc
- Gas Valves Unit for the supply and the exchange between the different gas flows allowing to obtain the best quality since the cut start, even on the thinner materials.
The real heart of these systems are the Cebora CP251G and CP450G (bevel) torches, with their relevant consumables (for which Cebora already deposited several patents), the cutting performances and service life of which represent the current state of the art. A particular care was devoted to the operating inexpensiveness, thus assuring an extremely reduced gas consumption in comparison to the competition, that makes the investment, in the Cebora HQC cutting systems, quickly amortizable.
The progressive increase of the demand for 3D cutting systems, implemented using either pantographs equipped with bevel cutting units or anthropomorphous robots, brought Cebora to develop a complete family of bevel torches with relevant consumables, that is the CP450G series, just devoted to the 3D cut, either for pantograph or for robot. The CP450G bevel torches are distinguished by dimensions and technical solutions expressly designed for these applications and allow space need as well as freedom and integration degrees that these same solutions require.
To the torches have also been added robot interfaces capable to satisfy any interconnection need: from the traditional analogic interfaces to the most modern and sophisticated digital ones, based on the main industrial BUS.
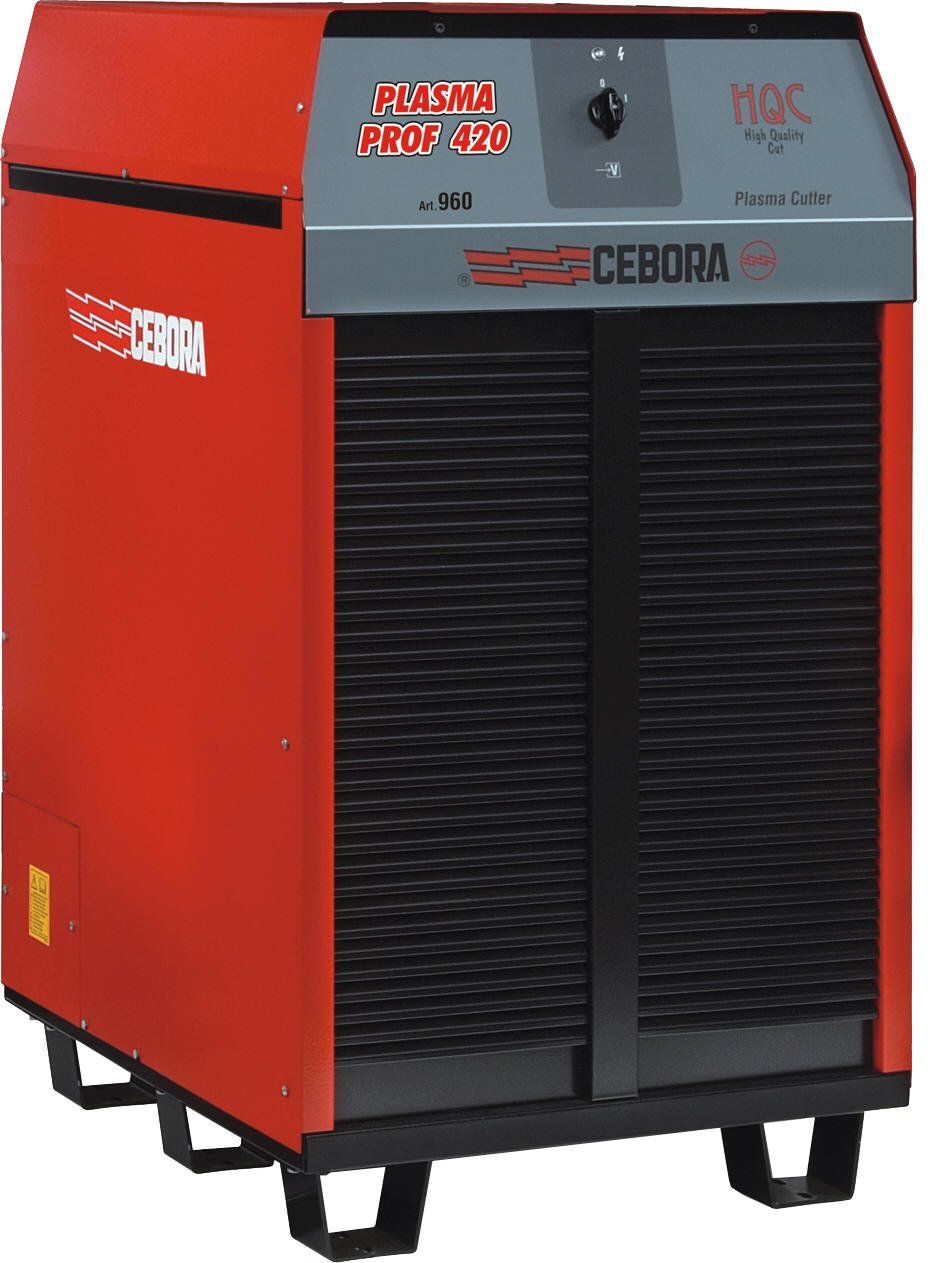
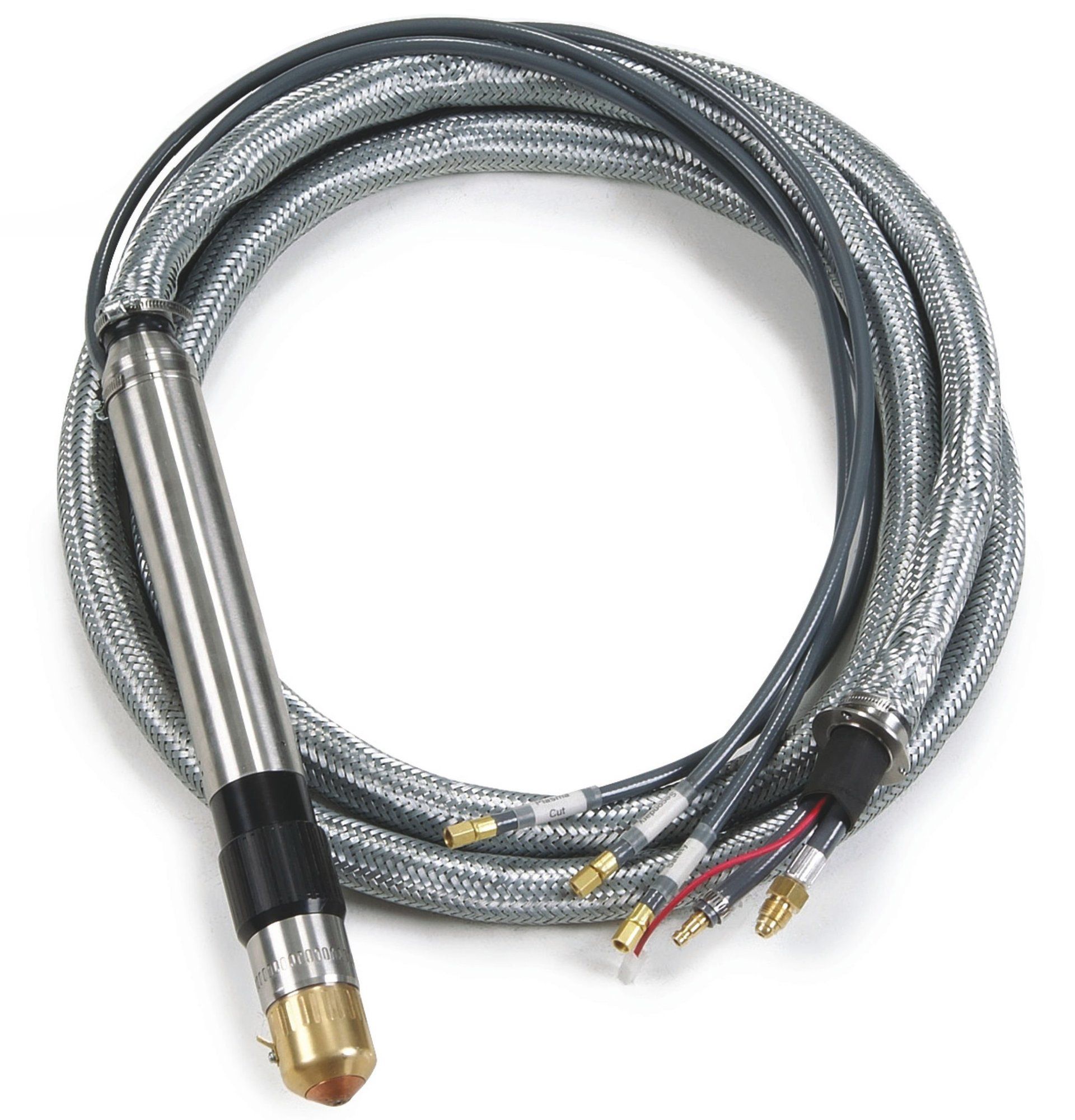
CP251G Plasma Torch (Art. 1237.05 1237.07 1237.50)
Genuine Cebora plasma cutting torch. High frequency ignition, water cooled
We carry the whole range of Cebora cutting torches.