Industrial Line Products
The Industrial line includes power sources - intended for professional use - for MIG, TIG and MMA welding, plasma cutting power sources and multi-purpose spotteres. The Cebora power sources of the Industrial line are manufactured with the latest technologies and strictly in compliance with the international standards in force.
MIG-MAG COMPACT EVOEVO 160 M COMBI (Art 495)
The Cebora EVO 160 M Combi MIG
welding power source is renowned for its extraordinary reliability, due to its simple design and the generous sizing of its subassemblies and components.
It is a single-phase power source conceived for MIG-MAG and flux-cored wire welding (5 Kg. coils diameter 200mm) and is suitable for the automotive repair, maintenance and small manufacturing industries.
The "no-gas" option makes it ideal for on-site works where cylinders are inconvenient to use.
The power source allows to choose among 7 welding current positions and is supplied with 3 m Cebora torch.
Complies with EN 61000-3-12.
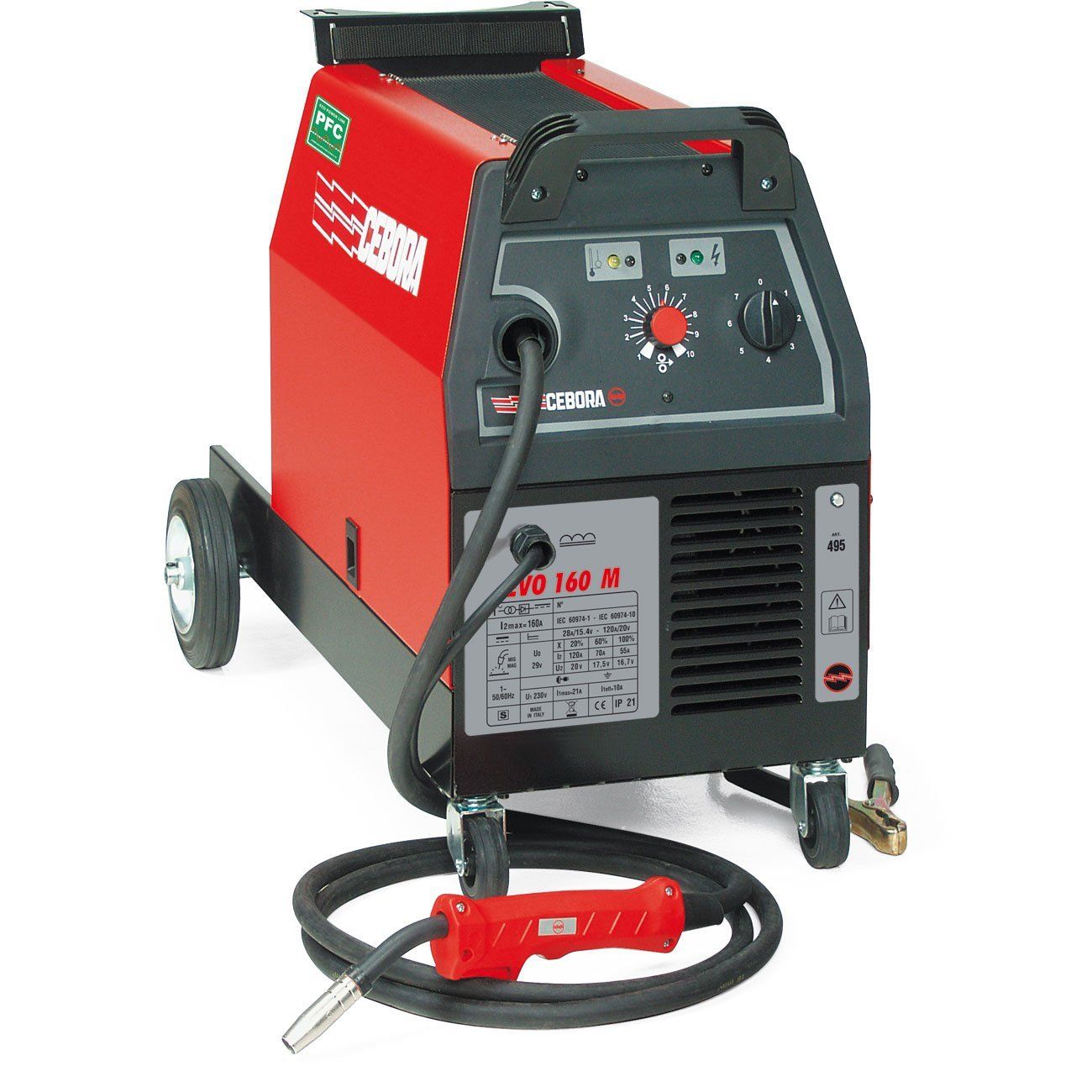
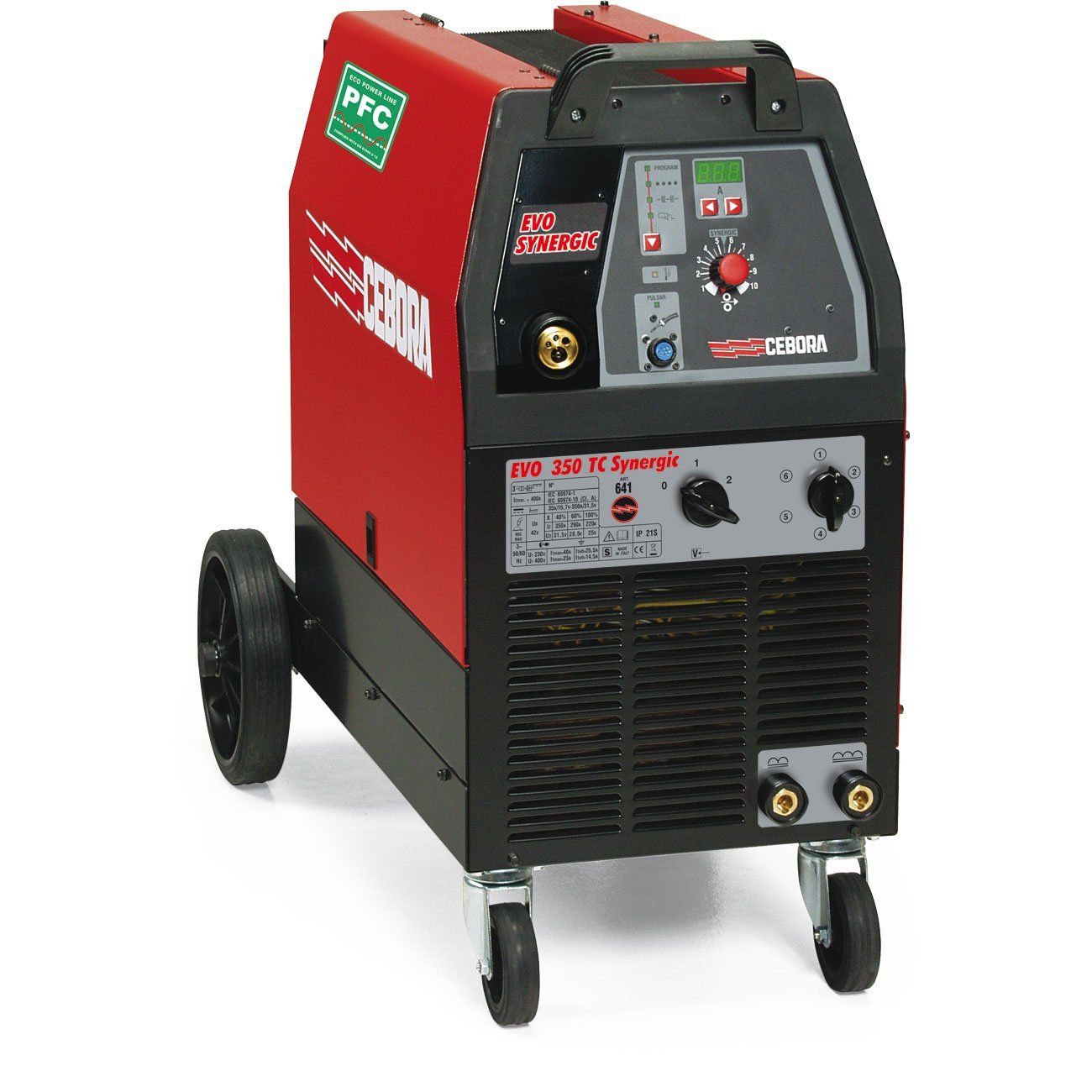
MIG-MAG - SYNERGIC COMPACT EVOEVO 350 TC SYNERGIC (Art 641)
The EVO synergic range is the result of product engineering that foresees not only a "product family look" but, mainly, a standardization of strategic components such as, for example, the control circuit, which is only one for all the models of the EVO range.
The EVO synergic range is made up of one single-phase power source EVO 200M synergic COMBI (Art. 622) and two three-phase power sources EVO 200T synergic (Art. 627) and EVO 350TC synergic (Art. 641) from 230A to 400A. The power source Art. 622 may also work with flux-cored wire.
The power sources are fitted with aluminium wire feeder (4 rollers model EVO 350TC synergic) and 12 welding current positions (16 positions model EVO 350TC synergic).
They have an adequate range of synergic curves in memory, and are
especially recommended for MIG brazing of galvanized sheet metal and high-strength steels.
Using the power source with the Cebora 2003 Push-Pull system torch makes the EVO SYNERGIC power sources also suitable for welding aluminium: connecting the Cebora 2003 Push-Pull system torch activates the specific synergic programs that Cebora has created for aluminium wires starting at a gauge of Ø 0.6.
The microprocessor used in the new control circuit makes it possible to upgrade, even over a long period, the synergic programs stored in the machine by means of the optional kit art. 136.
Three different types of torches may be used: Standard MIG, Push Pull 2003, and Spool Gun (only the manual function is active with the Spool Gun). The EVO synergic power sources are suitable for use in the automotive and for light/medium metal fabrication.
Complies with EN 61000-3-12.
MIG-MAG - SYNERGIC EVO WITH SEPERATE WIRE FEEDEVO 350 TS SYNERGIC (Art 643)
The EVO synergic range, in the version with separate wire feeder, is the result of product engineering that foresees a standardization of strategic components such as, for example, the control circuit, which is only one for all the models of the EVO range.
The EVO TS synergic range is made up of two three-phase power sources of 350 and 450A at 40% respectively.
The two power sources may be equipped, at the customer's discretion, with 2-roll (art. 1652, with Ø 30 mm rollers) or 4-roll (art. 1662, with Ø 40 mm rollers) wire feed units capable of reaching wire speeds of 20 and 24 m/min, respectively, both fitted with digital ammeter/volt meter and equipped with a "burn-back" adjustment device, which encourages smooth restarting thanks to the wire speed control during arc shut-off.
The power sources have an adequate range of synergic curves in memory for mild steel, stainless steel, aluminium, MIG brazing and flux cored wire (the microprocessor in the control circuit makes it possible to upgrade, even over a long period, the synergic programs stored in the machine) by means of the optional Kit art. 136.
The power sources are designed to accept the optional torch cooling unit. Complies with EN 61000-3-12.
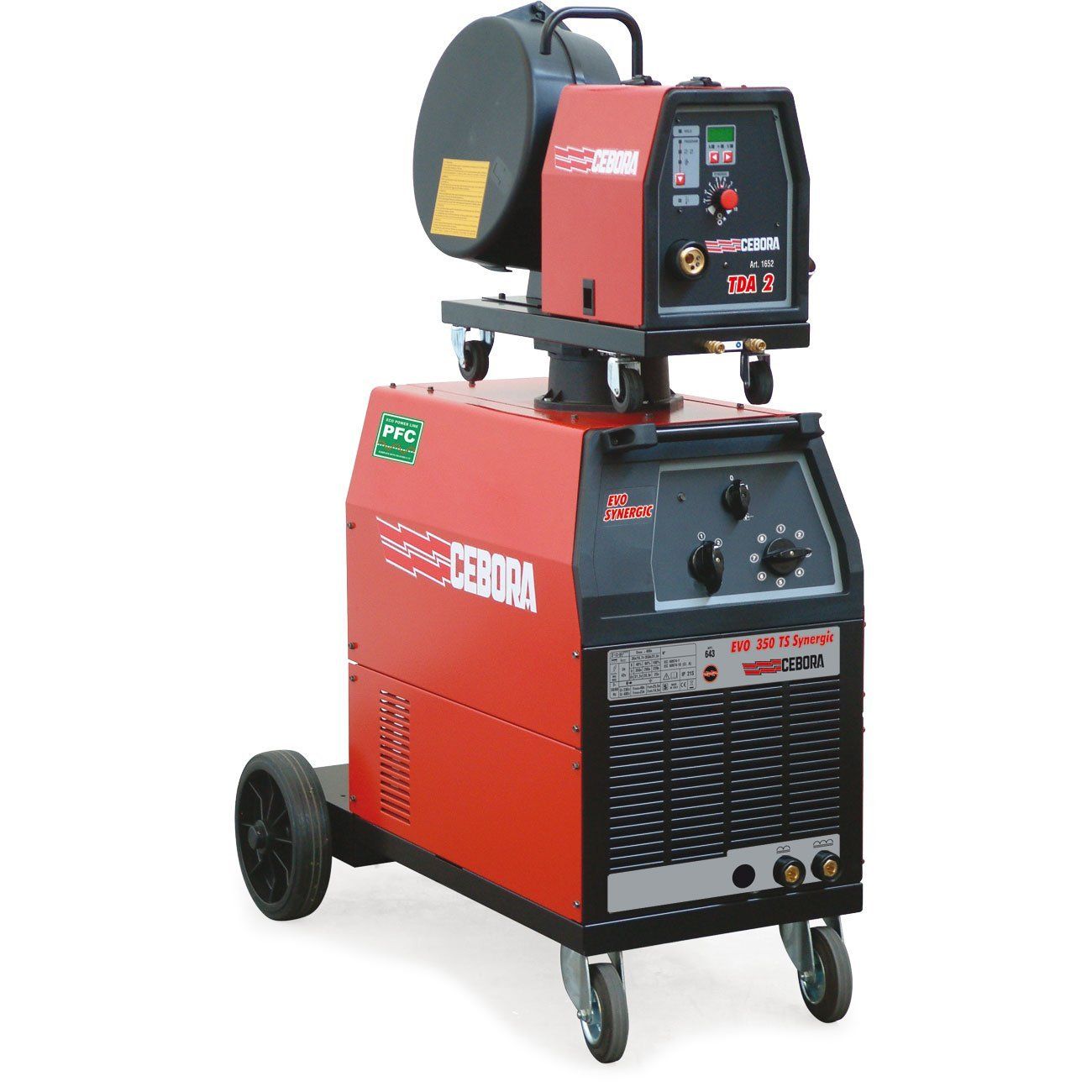
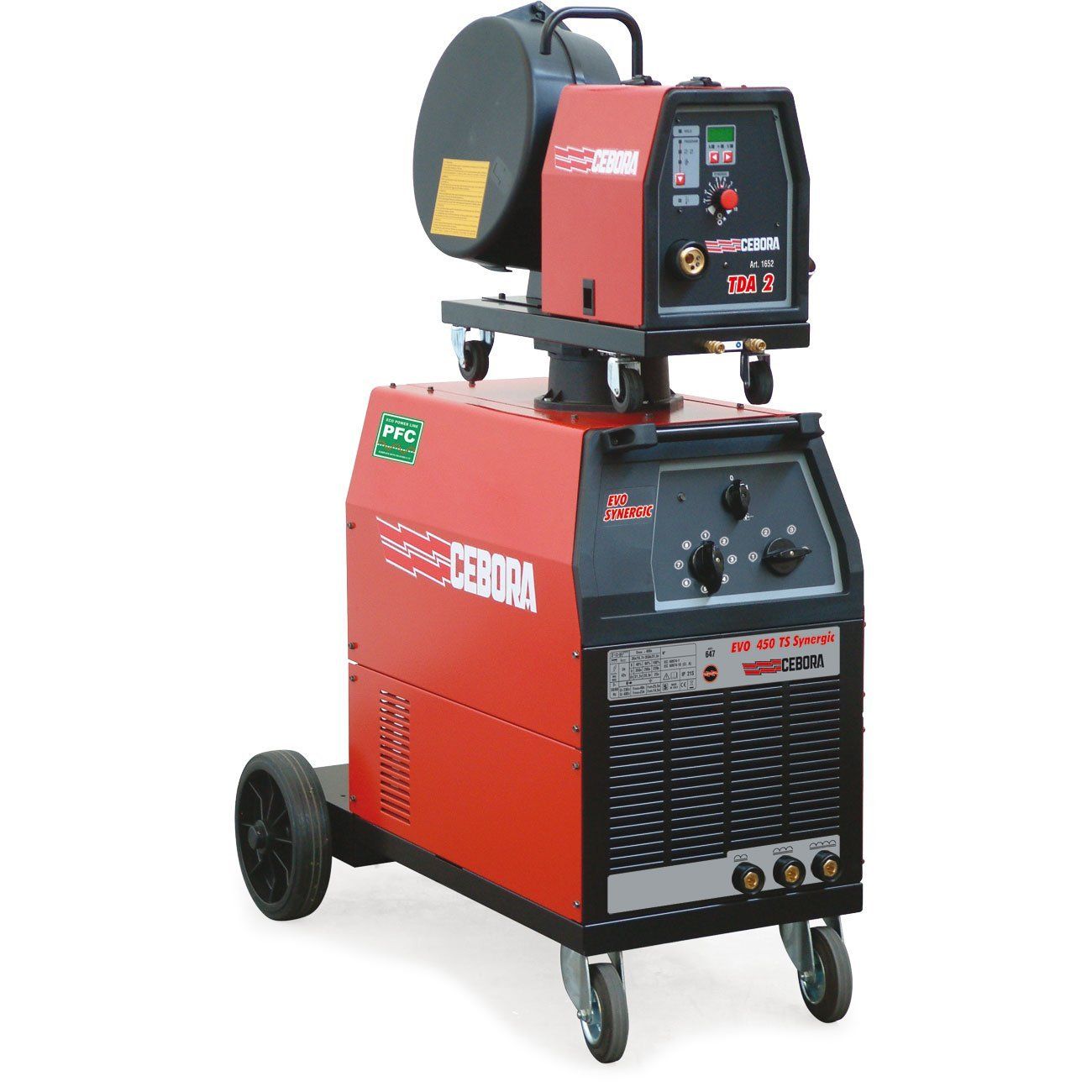
EVO 450 TS SYNERGIC (Art 647)
The EVO synergic range, in the version with separate wire feeder, is the result of product engineering that foresees a standardization of strategic components such as, for example, the control circuit, which is only one for all the models of the EVO range.
The EVO TS synergic range is made up of two three-phase power sources of 350 and 450A at 40% respectively.
The two power sources may be equipped, at the customer's discretion, with 2-roll (art. 1652, with Ø 30 mm rollers) or 4-roll (art. 1662, with Ø 40 mm rollers) wire feed units capable of reaching wire speeds of 20 and 24 m/min, respectively, both fitted with digital ammeter/volt meter and equipped with a "burn-back" adjustment device, which encourages smooth restarting thanks to the wire speed control during arc shut-off.
The power sources have an adequate range of synergic curves in memory for mild steel, stainless steel, aluminium, MIG brazing and flux cored wire (the microprocessor in the control circuit makes it possible to upgrade, even over a long period, the synergic programs stored in the machine) by means of the optional Kit art. 136. The power sources are designed to accept the optional torch cooling unit.
Complies with EN 61000-3-12.
INVERTER SYNERGIC MIG-MAGMONO STAR MIG 1620/M SYNERGIC (Art 304)
Inverter single-phase synergic power source for MIG-MAG welding, with 2-roller Cebora wire feed unit. The power source features synergic curves for iron wire Ø 0.6 /0.8 mm and Ø 0.9 mm flux cored wire. The cored wires can be welded, either with or without shielding gas, by simple polarity reverse. A package of optional curves for AlMg, AlSi, stainless steel and CuSi3 is available too. The LCD panel
allows the operator to read, on three lines, wire and gas type, current and thickness, voltage and wire speed.
It is a specially versatile power source, suitable for various applications, especially repairs, maintenance and basic car body repairs, marked out by a low electrical input (PFC). The Euro connection allows to use either a standard MIG torch (art. 1246) or a "professional" type torch (art. 1638), particularly suitable for flux cored wire welding. An optional dedicated transport trolley (art. 1653), particularly compact and handy, is available too.
Complies with EN 61000-3-12.
The power source can also be powered by motor-driven generators of adequate power (min. 6 KVA).
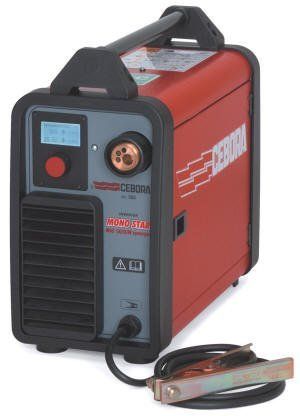
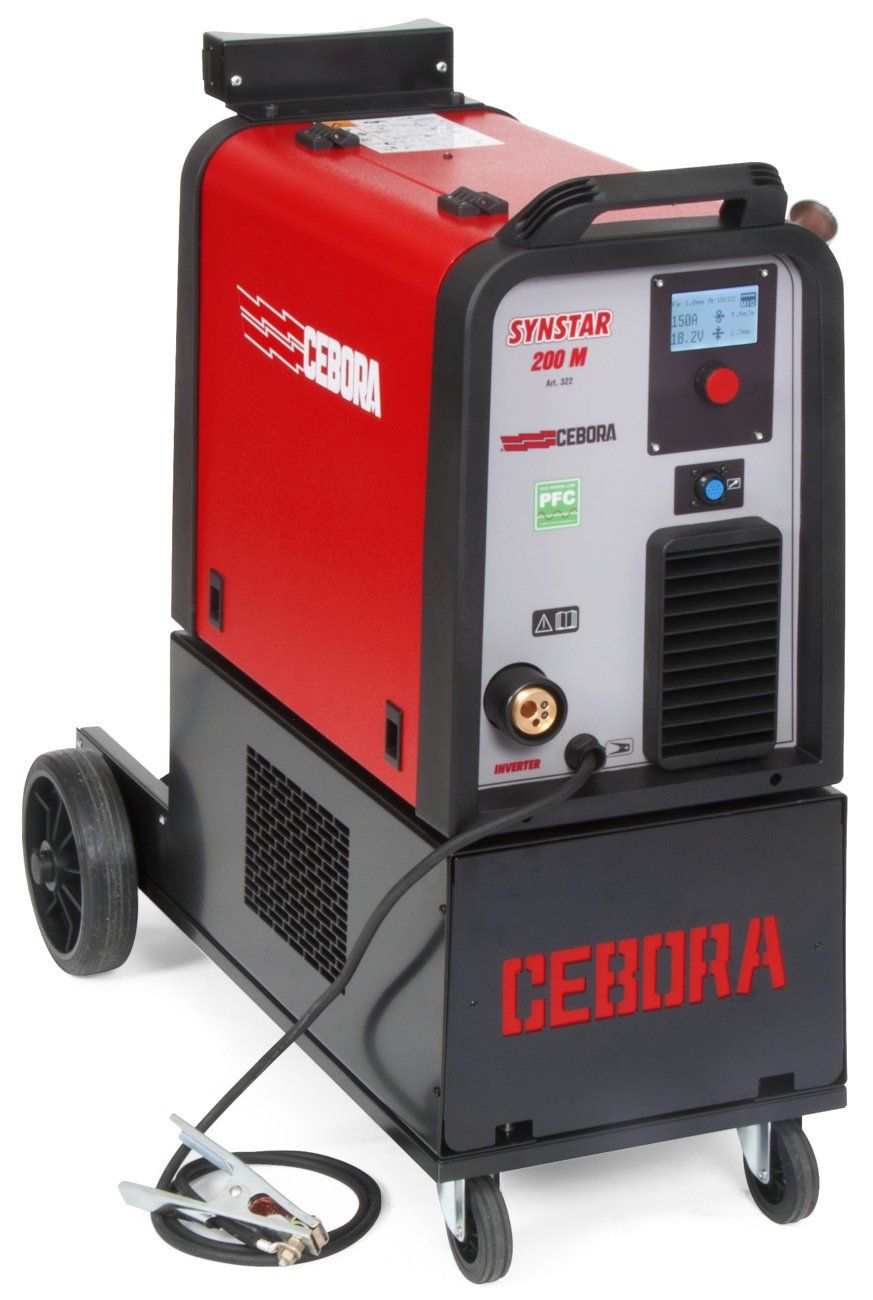
INVERTER SYNERGIC MIG-MAG (with optional pulse)SYNSTAR 200 M (Art 322)
The new SYNSTAR 200 M is an inverter single-phase synergic power source for MIG-MAG welding, with 2-roller Cebora wire feed unit.
The power source features synergic curves for Ø 0.6 / 0.8 / 0.9 / 1.0 mm solid wire as well as for Ø 0.9 mm fl ux cored wire. The cored wires can be welded either with or without shielding gas, by simple polarity reverse.
As optional is available a pulse function upgrade (Art.238) that allows to activate devoted pulse synergic curves for mild steel, stainless steel, aluminium and Cusi3. The LCD panel allows the operator to read wire and gas type, current and thickness, voltage and wire speed. The power source is complete with many functions adjustable from control panel like: Arc Length, 2 time, 4 time, Spot Time, Pause Time, Inductance, Burn Back, Soft Start etc.
It is a specially versatile power source, suitable for various applications, especially repairs, maintenance and car body repairs, marked out by a low electrical input (PFC). The Euro connector allows to use either a standard MIG torch or the Cebora Push-Pull 2003 torch. It is possible to work with two different types of coils: Ø 200 mm or Ø 300 mm.
Complies with en 61000-3-12.
SYNSTAR 200 T (Art 323)
The new SYNSTAR 200 T is an inverter three-phase synergic power source for MIG-MAG welding, with 2-roller Cebora wire feed unit.
The power source features synergic curves for Ø 0.6 / 0.8 / 0.9 / 1.0 mm solid wire (aluminium also Ø 1.2 mm) as well as for Ø 0.9 mm flux cored wire. The cored wires can be welded either with or without shielding gas, by simple polarity reverse.
As optional is available a pulse function upgrade (Art. 238) that allows to activate devoted pulse synergic curves for mild steel, stainless steel, aluminium and CuSi3.
The LCD panel allows the operator to read wire and gas type, current and thickness, voltage and wire speed.
The power source is complete with many functions adjustable from control panel like: Arc Length, 2 times / 4 times, Spot Time, Pause Time, Inductance, Burn Back, Soft Start, pre-gas, post-gas etc.
It is a specially versatile power source, suitable for various applications, in particular for light - medium metal works, marked out by a low electrical input (PFC). The Euro connector allows to use either a standard MIG torch or the Cebora Push-Pull 2003 torch.
It is possible to work with two different types of coils: Ø 200 mm or Ø 300 mm.
Complies with en 61000-3-12.
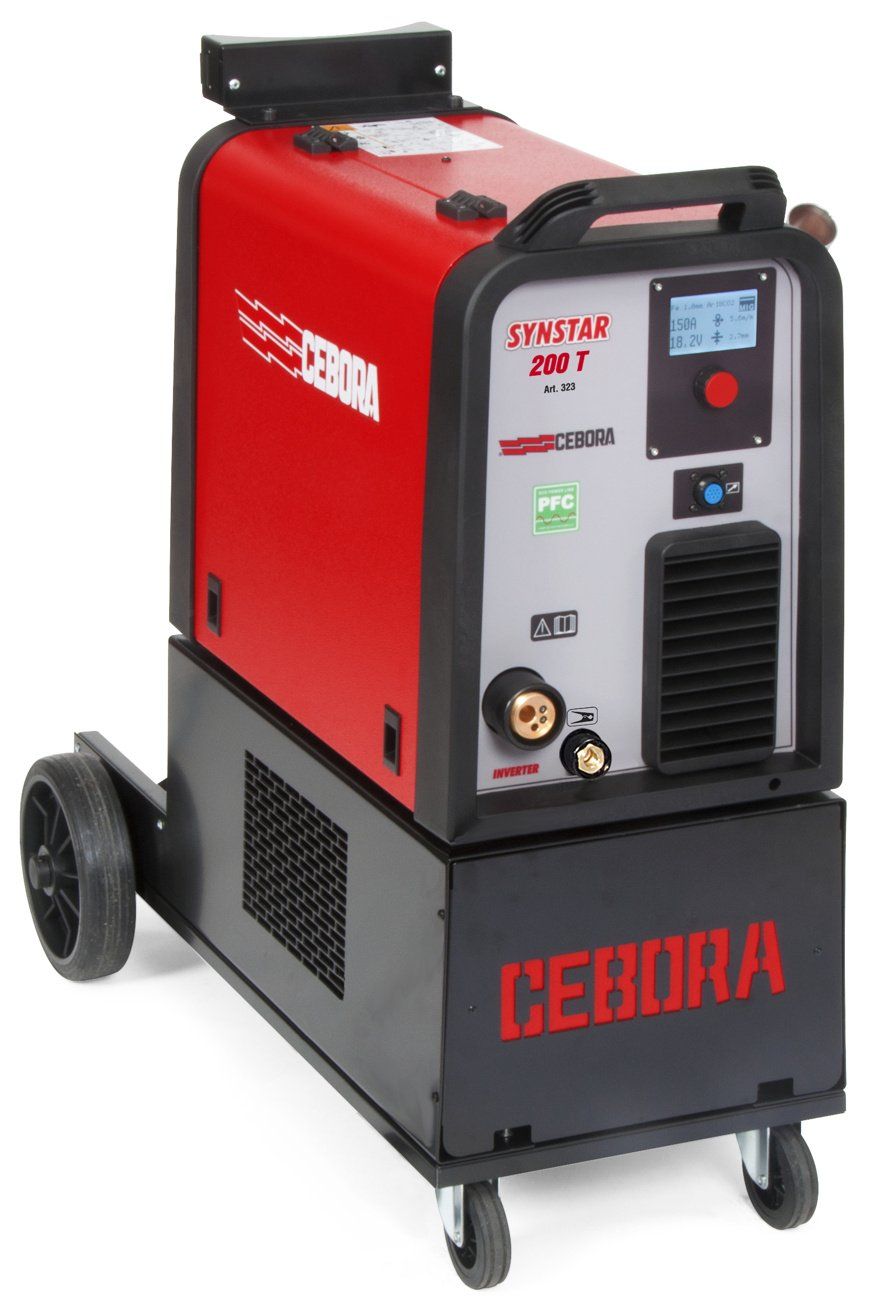
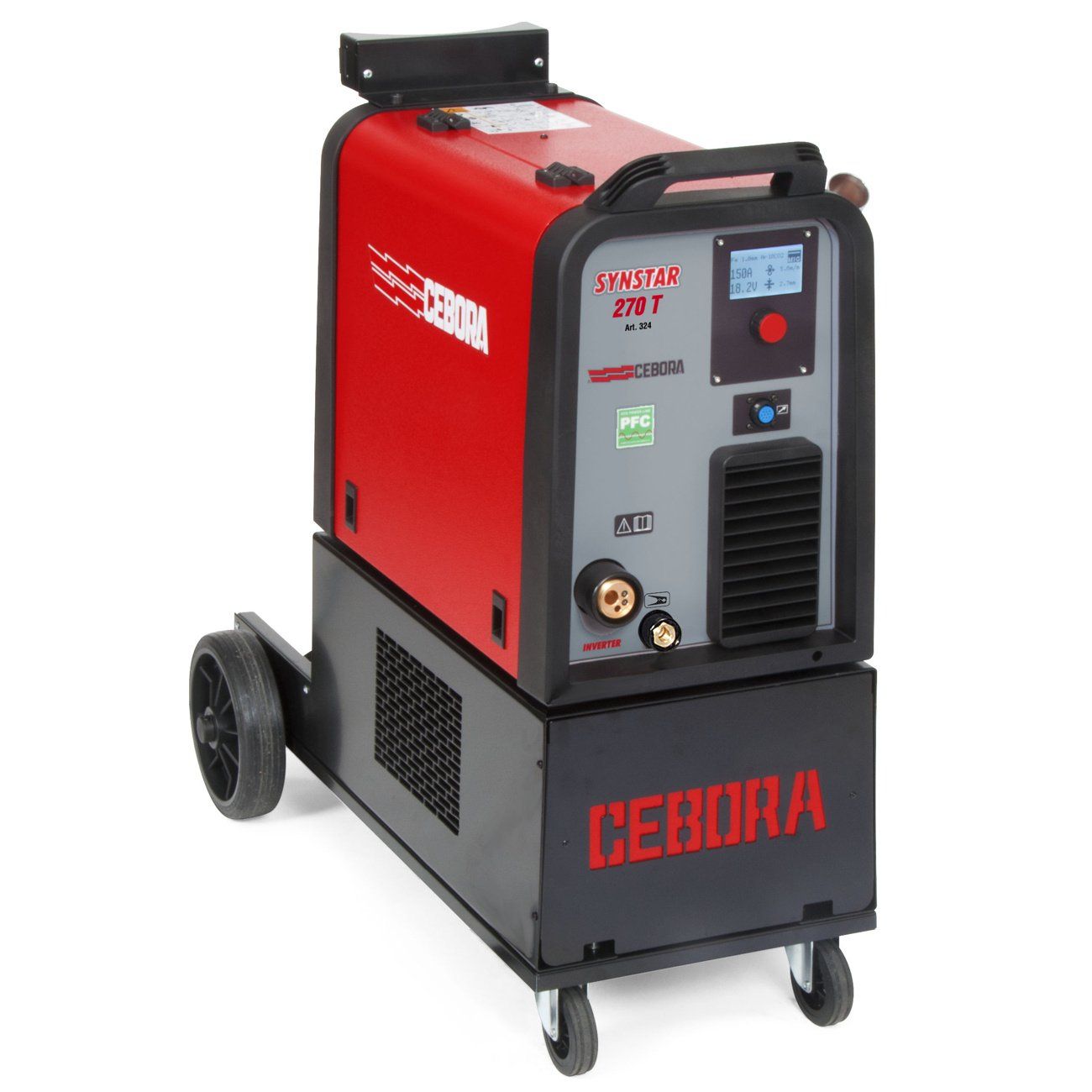
SYNSTAR 270 T (Art 324)
The new SYNSTAR 270 T is an inverter three-phase synergic power source for MIG-MAG welding, with 4-roller Cebora wire feed unit.
The power source features synergic curves for Ø 0.6/0.8/0.9/1.0/1.2mm solid wire.
With the optional pulse function upgrade (Art. 238), that allows to activate devoted pulse synergic curves for mild steel, stainless steel, aluminium and CuSi3, the SYNSTAR 270 T has more than 60 welding programs available.
This power source can be equipped with 3 different types of torch:
- 4 m air cooled push-pull torch art. 2003 (160A at 40%)
- 3.5 m air cooled Cebora torch art. 1242 (280A at 60%)
- 3.5 m water cooled Cebora torch art. 1241 (380A at 60%)
The LCD panel allows the operator to read wire and gas type, current and thickness, voltage and wire speed.
The power source is complete with many functions adjustable from the control panel such as: Arc Length, short or pulsed welding process, 2 times / 4 times, Spot Time, Pause Time, Inductance, push-pull force, Burn Back, Soft Start, pre-gas and post gas.
An optional cooling unit (art. 1681) is also available. It is a specially versatile power source, suitable for various applications, in particular for medium metal works, marked out by a low electrical input (PFC).
Complies with EN 61000-3-12.
INVERTER SYNERGIC MULTIPROCESS MIG-MAGTRI STAR MIG 1636/M (Art 298)
TRI-STAR is a single-phase multipurpose inverter power source, suitable for MIG/MAG, MMA (stick electrode) and TIG (with "Cebora lift ignition") welding. Cebora developed it with the concept of applying mobility and multipurpose to welding. The simple and user friendly control panel allows quick process selection and displays the selection on the front panel, (MIG/MAG, MMA and DC TIG).
In the MIG/MAG mode, it is possible to select a synergic program according to the wire type and diameter as well as the shielding gas to be used. The power source has 11 synergic curves optimized for steel (Ø 0.6 - 1), stainless steel (Ø 0.8), aluminium (Ø 1), MIG brazing (Ø 0.8) and flux cored wire (Ø 0.9). The synergic programs for steel allow working with either mixed gasses or 100% CO2. A dedicated control is provided for fine tuning the arc length. The MIG/MAG torch is specific for this power source and is also available in a special version for use mainly with flux-cored wire (art.1636).
In the MMA welding mode, the power source can weld electrodes up to Ø 3.25.
The TRI-STAR, with its low weight and compact dimensions, added to it's multi-process capability of welding in MIG/MAG,TIG and MMA mode make this an ideal machine for maintenance, repair, installation and on site welding.
Of course the Tri-Star is a great workshop tool also! The low electrical input from a single phase supply make the use of this machine possible in a wide range of the environments. The compliance with EN 61000-3-12
brings substantial energy saving and a wide supply voltage tolerance (+15% / -20%). The power source can be powered by motor generators of adequate power (Min. 6 KVA).
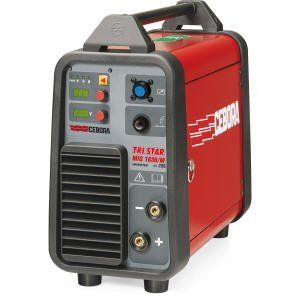
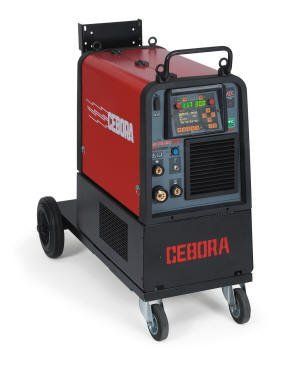
INVERTER SYNERGIC MULTIPROCESS MIG-MAG (with optional pulse and double pulse)EVO SPEED STAR 380 TC (Art 318)
EVO SPEED STAR 380 TC
is a compact multi-process inverter three phase welding power source (MIG-MAG, MMA, DC TIG with “Lift by Cebora” contact ignition system), with synergic control which allows controlling the welding conditions through just one variable, all the others being pre-set by Cebora and dependent on it.
It is an innovatory power source, distinguished by specific functions and features that make it particularly competitive and suitable for all those applications that require a high productivity, for instance in the heavy metal work, constructions, shipbuilding etc.
The power source, which assures an excellent arc ignition (strikes) also features:
- HD (HIGH DEPOSIT) synergic programs
that allow to increase the wire speed (AMP) without changing the voltage (VOLT), consequently increasing the level of deposited material, thus making the welding process more economical and competitive.
- A specific MIG ROOT welding program, for fi rst pass or high quality vertical root pass such as, for instance, root pass on pipes (with a maximum 5 mm gap).
- Possibility to work with long stick-outs thanks to an optimization of the control and of the arc steadiness when the operator must work in particular positions (like V-shape). In the Evo Speed Star line are also available the following optional functions:
- TIG PULSE, art. 234
- Double Level, art. 233
- Pulse, art. 231
- The DOUBLE PULSE
function is obtained by implementing in the power source both the DOUBLE LEVEL (art. 233) and the PULSE (art. 231) optional functions.
The new SOUND DIGIBOX MIG P4 control panel, with OLED technology, has a wide display which allows the operator to easily select and set the different welding modes / options available in the power source. It also allows to always have clearly displayed the current welding parameters (selected process, type and diameter of the used wire, shielding gas etc.).
The possibility to access the adjustment and the control of a wide range of power source parameters and functions allows the operator to optimize the use of the machine in the selected welding process.
The software and the synergic programs can be updated in the power sources through either RS232 or a USB port.
The power source is equipped with a 4 roller (Ø 30 mm) wire feed device in aluminium. The optional GRV12 torch cooling unit is also available. The high efficiency of the ventilation of the sub-units allows achieving performance levels in continuous mode only slightly below those provided at the maximum current.
Complies with the EN 61000-3-12 standard.
EVO SPEED STAR 380 TS (Art 319)
EVO SPEED STAR 380 TS
is a multi-process inverter three phase welding power source (MIG-MAG, MMA, DC TIG with “Lift by Cebora” contact ignition system) with separate wire feeder, with synergic control which allows controlling the welding conditions through just one variable, all the others being pre-set by Cebora and dependent on it.
It is an innovatory power source,
distinguished by specific functions and features that make it particularly competitive and suitable for all those applications that require a high productivity, for instance in the heavy metal work, constructions, shipbuilding etc.
The power source, which assures an excellent arc ignition (strikes) also features:
- HD (HIGH DEPOSIT) synergic programs
that allow to increase the wire speed (AMP) without changing the voltage (VOLT), consequently increasing the level of deposited material, thus making the welding process more economical and competitive.
- A specific MIG ROOT welding program, for fi rst pass or high quality vertical root pass such as, for instance, root pass on pipes (with a maximum 5 mm gap).
- Possibility to work with long stick-outs thanks to an optimization of the control and of the arc steadiness when the operator must work in particular positions (like V-shape). In the Evo Speed Star line are also available the following optional functions:
- TIG PULSE, art. 234
- Double Level, art. 233
- Pulse, art. 231
- The DOUBLE PULSE
function is obtained by implementing in the power source both the DOUBLE LEVEL (art. 233) and the PULSE (art. 231) optional functions.
The new SOUND DIGIBOX MIG P4 control panel, with OLED technology, has a wide display which allows the operator to easily select and set the different welding modes / options available in the power source. It also allows to always have clearly displayed the current welding parameters (selected process, type and diameter of the used wire, shielding gas etc.).
The possibility to access the adjustment and the control of a wide range of power source parameters and functions allows the operator to optimize the use of the machine in the selected welding process.
The software and the synergic programs can be updated in the power sources through either RS232 or a USB port.
The power source is equipped with a 4 roller (Ø 30 mm) wire feed device in aluminium.
The optional GRV12 torch cooling unit is also available.
The high efficiency of the ventilation of the sub-units allows achieving performance levels in continuous mode only slightly below those provided at the maximum current.
Complies with the EN 61000-3-12 standard.
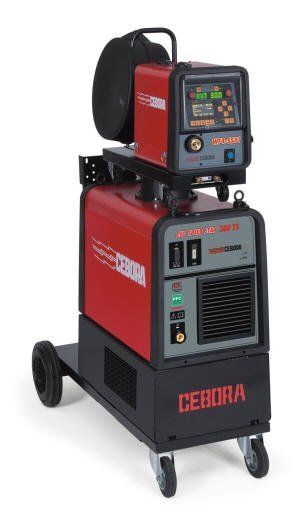
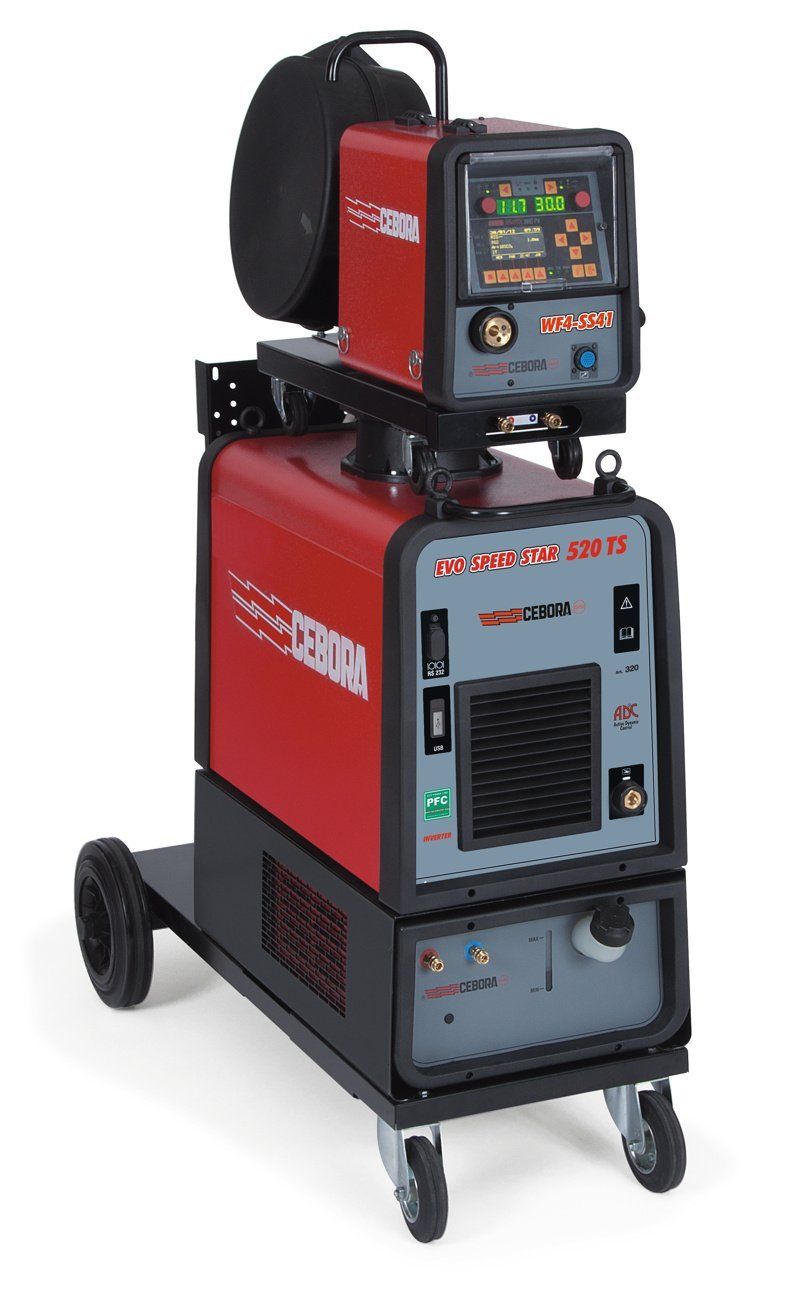
EVO SPEED STAR 520 TS (Art 320)
EVO SPEED STAR 520 TS
is a multi-process inverter three phase welding power source (MIG-MAG, MMA, DC TIG with “Lift by Cebora” contact ignition system) with separate wire feeder, with synergic control which allows controlling the welding conditions through just one variable, all the others being pre-set by Cebora and dependent on it.
It is an innovatory power source, distinguished by specific functions and features that make it particularly competitive and suitable for all those applications that require a high productivity, for instance in the heavy metal work, constructions, shipbuilding etc.
The power source, which assures an excellent arc ignition (strikes) also features:
- HD (HIGH DEPOSIT) synergic programs
that allow to increase the wire speed (AMP) without changing the voltage (VOLT), consequently increasing the level of deposited material, thus making the welding process more economical and competitive.
- a specific MIG ROOT welding program, for fi rst pass or high quality vertical root pass such as, for instance, root pass on pipes (with a maximum 5 mm gap).
- Possibility to work with long stick-outs
thanks to an optimization of the control and of the arc steadiness when the operator must work in particular positions (like V-shape).
In the Evo Speed Star line are also available the following optional functions:
The new SOUND DIGIBOX MIG P4 control panel, with OLED technology, has a wide display which allows the operator to easily select and set the different welding modes / options available in the power source. It also allows to always have clearly displayed the current welding parameters (selected process, type and diameter of the used wire, shielding gas etc.).
The possibility to access the adjustment and the control of a wide range of power source parameters and functions allows the operator to optimize the use of the machine in the selected welding process.
The software and the synergic programs can be updated in the power sources through either RS232 or a USB port.
The power source is equipped with a 4 roller (Ø 40 mm) wire feed device in aluminium, as well as with a GRV12 torch cooling unit.
The high efficiency of the ventilation of the sub-units allows achieving performance levels in continuous mode only slightly below those provided at the maximum current.
Complies with the EN 61000-3-12 standard.
PULSED INVERTER SYNERGIC MIG-MAGSOUND MIG 2060/MD STAR DOUBLE PULSE (Art 301)
The SOUND MIG 2060/MD STAR DOUBLE PULSE
(art. 301) is a MIG-MAG inverter synergic welding machine, with pulse and double pulse functions, capable of welding and MIG brazing galvanized sheet metal, high-strength steel and aluminium alloys.
It is a power source that , thanks to the synergic pulsed technology used, is especially recommended for welding aluminium. It also offers a complete range of synergic programs for aluminium wires. Using the power source with the Cebora 2003 Push-Pull torch makes it possible to achieve optimum welding starting with Ø0.6-gauge wires.
The SOUND MIG 2060/MD STAR power source also contains saved synergic curves corresponding the CuSi 3% and CuAl8 (AlBz8) wires used for MIG brazing and welding, thus also making the power source especially suitable for MIG brazing and welding galvanized sheet metal and high-strength steels.
Two types of torches may be used with the SOUND MIG 2060/MD STAR power source: Standard MIG and Cebora Push-Pull 2003. It is also possible to work with two different types of coils: Ø 200 mm (standard version with trolley Art. 1656) or Ø 300 mm (with coil kit art. 114 and trolley art. 1656).
The power source is standard-equipped with a wide range of synergic curves in memory.
The compliance with EN 61000-3-12
brings substantial energy saving and a wide supply voltage tolerance (+15% / -20%).
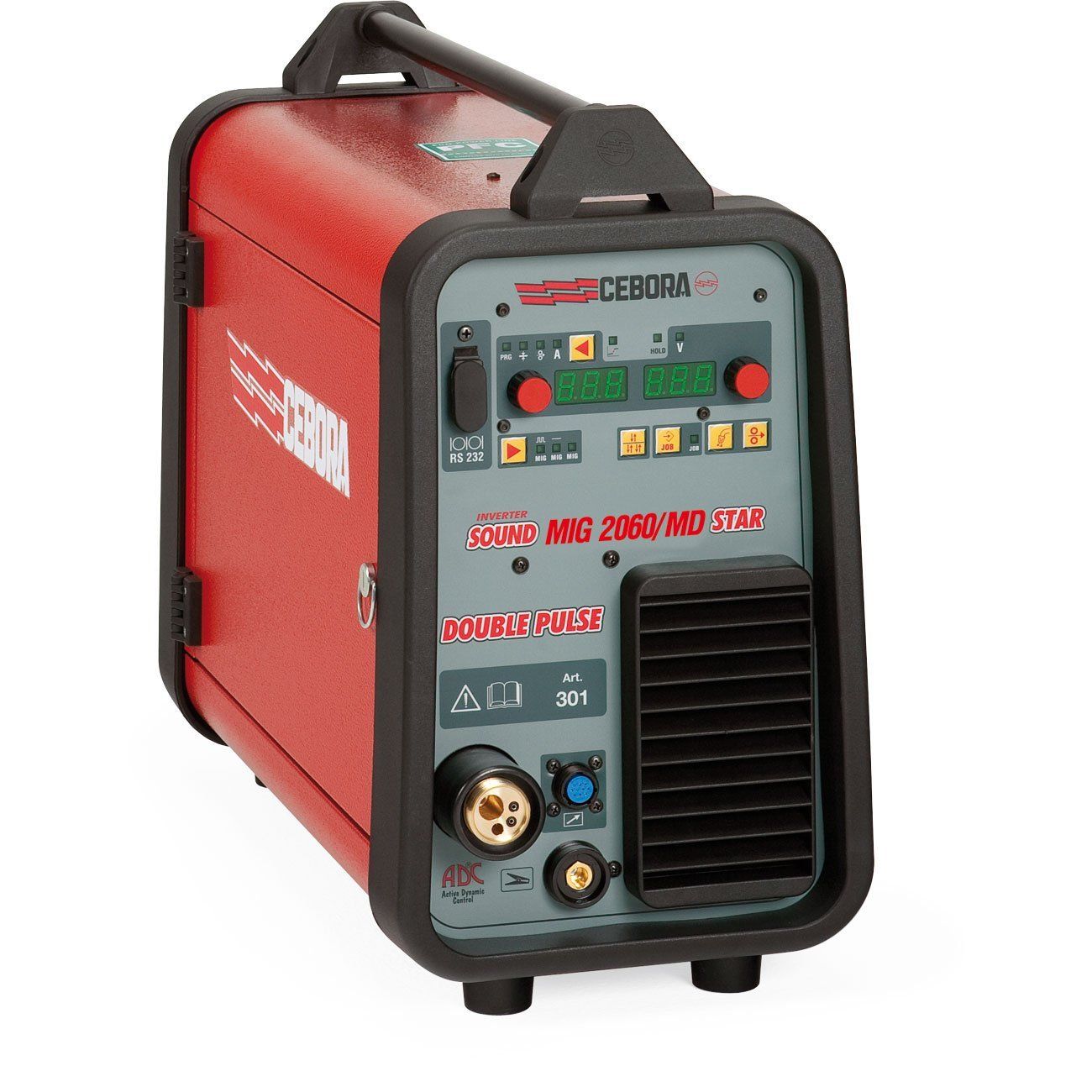
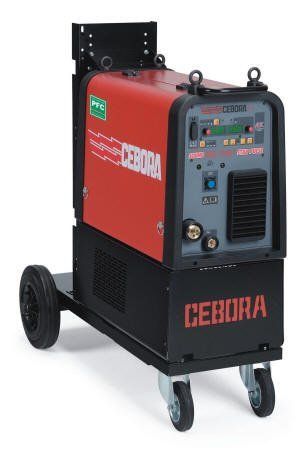
SOUND MIG SYNERGIC 2740/T STAR PULSE (Art 307)
Inverter three-phase synergic pulsed and (optional) double pulsed power source, designed for high quality continuous wire (MIG-MAG, PULSED SYNERGIC MIG) welding , with 4-roller Cebora wire feed unit in aluminium.
The power source features a broad range of synergic curves relating to the most common operating conditions in welding.
It is a power source featuring an optimal performance/ quality/price ratio and is specially versatile, suitable for various applications.
With the Sound MIG Synergic 2740/T Star Pulse power source it is possible to use alternately 3 types of torch: 4 m air cooled Cebora Push Pull Up/Down torch art. 2003.39, to be used together with the Push Pull interface kit (art. 126), 3.5 m water cooled Cebora 380A torch (art. 1241) and 3.5 m air cooled Cebora 280A torch (art. 1242).
The compliance with EN 61000-3-12
brings substantial
energy saving and a wide supply voltage tolerance (+15% / -20%).
MULTIPROCESS (MIG - TIG - MMA)TRI STAR MIG 1636/M (Art 298)
TRI-STAR is a single-phase multipurpose inverter power source, suitable for MIG/MAG, MMA (stick electrode) and TIG (with "Cebora lift ignition") welding. Cebora developed it with the concept of applying mobility and multipurpose to welding. The simple and user friendly control panel allows quick process selection and displays the selection on the front panel, (MIG/MAG, MMA and DC TIG).
In the MIG/MAG mode, it is possible to select a synergic program according to the wire type and diameter as well as the shielding gas to be used. The power source has 11 synergic curves optimized for steel (Ø 0.6 - 1), stainless steel (Ø 0.8), aluminium (Ø 1), MIG brazing (Ø 0.8) and flux cored wire (Ø 0.9). The synergic programs for steel allow working with either mixed gasses or 100% CO2.
A dedicated control is provided for fine tuning the arc length. The MIG/MAG torch is specific for this power source and is also available in a special version for use mainly with flux-cored wire (art.1636). In the MMA welding mode, the power source can weld electrodes up to Ø 3.25. The TRI-STAR, with its low weight and compact dimensions, added to it's multi-process capability of welding in MIG/MAG,TIG and MMA mode make this an ideal machine for maintenance, repair, installation and on site welding.
Of course the Tri-Star is a great workshop tool also! The low electrical input from a single phase supply make the use of this machine possible in a wide range of the environments. The compliance with EN 61000-3-12
brings substantial energy saving and a wide supply voltage tolerance (+15% / -20%). The power source can be powered by motor generators of adequate power (Min. 6 KVA).
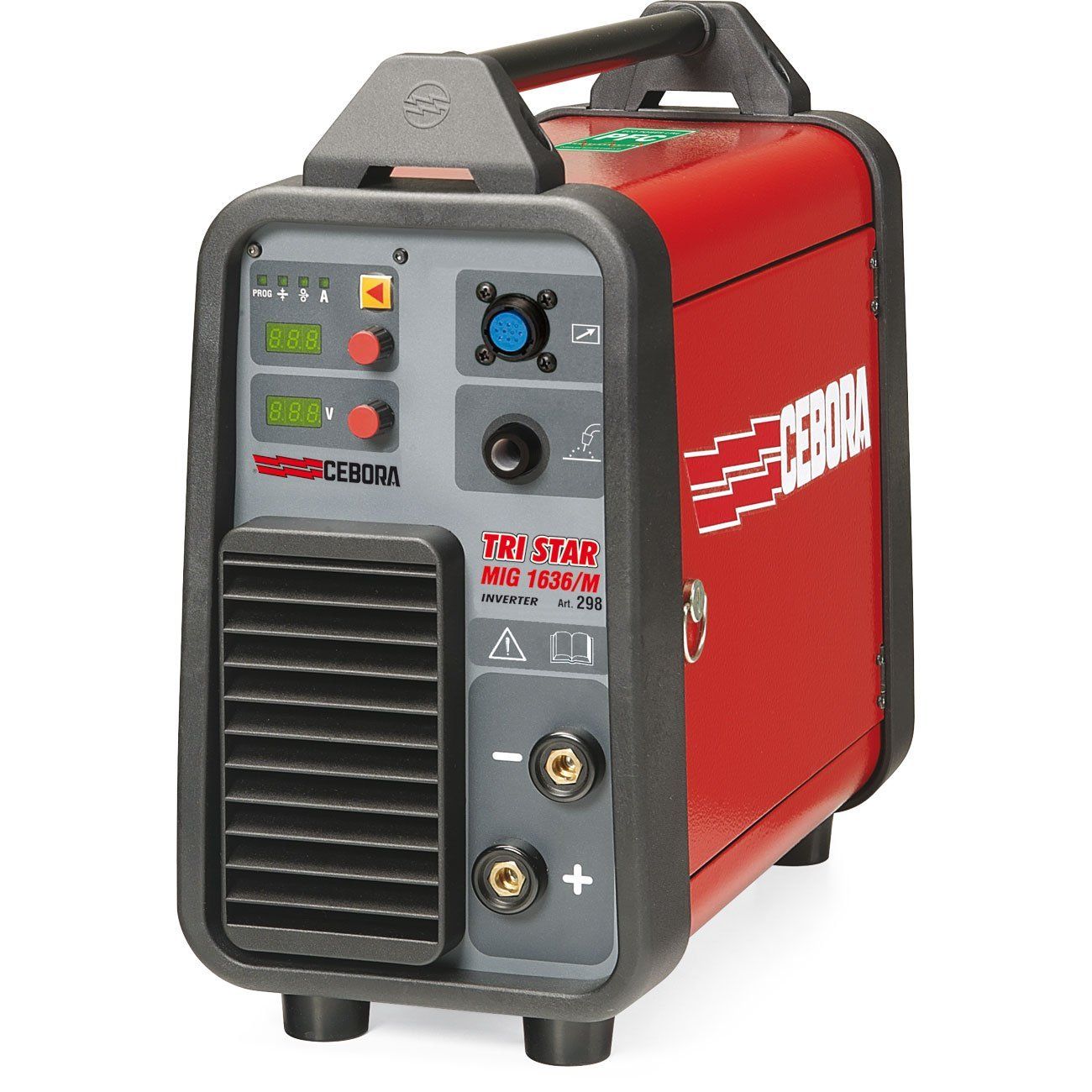
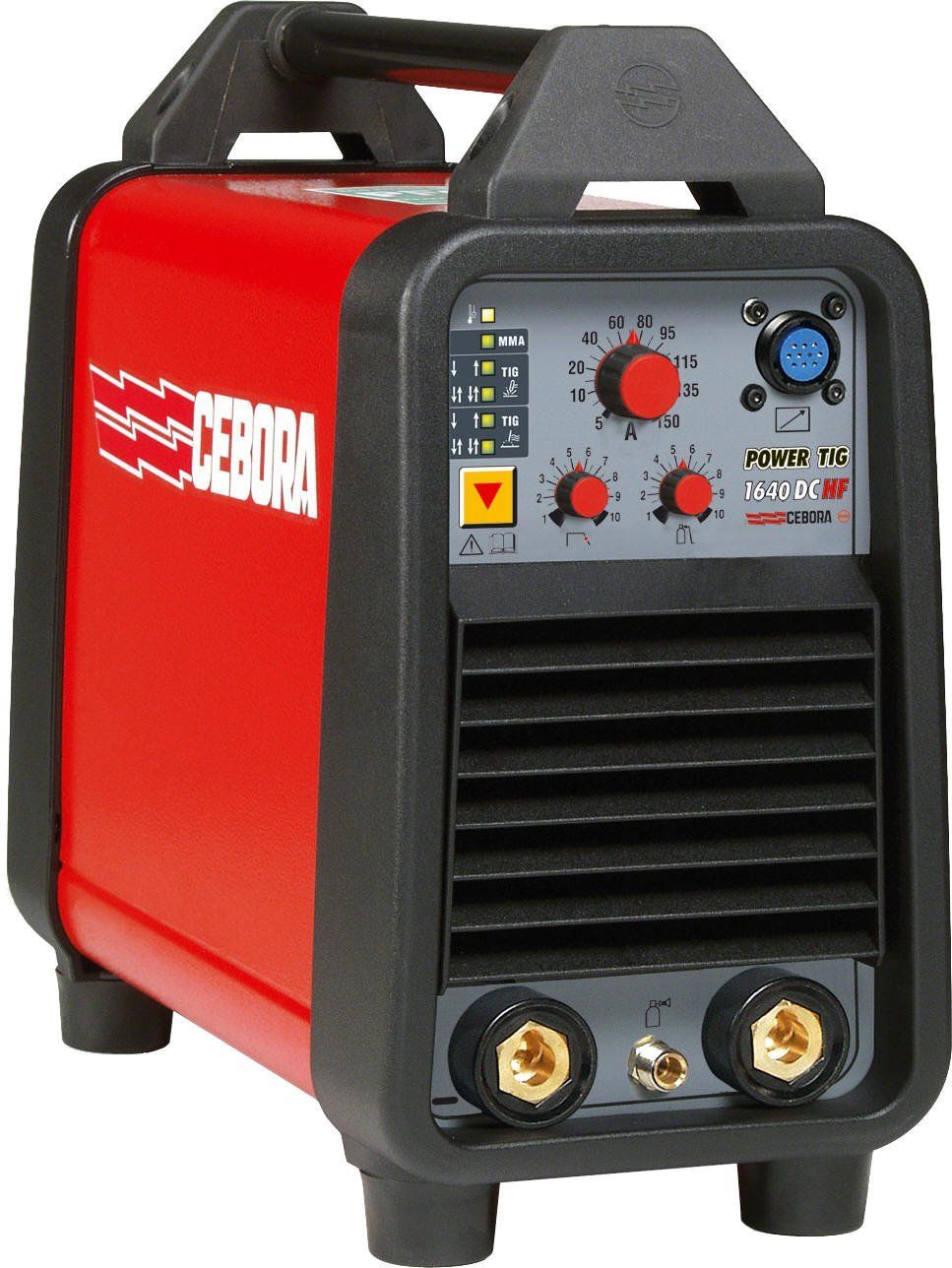
TIG DC INVERTERPower TIG 1640 DC-HF - TIG DC Inverter (Art 264)
The POWER TIG 1640 DC HF
is a DC TIG/MMA welding power source, inverter technology. In TIG mode the arc is started either in HF or with the Cebora lift system. It features a 2 stage/4 stage selection key, while the remote control device allows to connect a foot control or, alternatively, to work with a torch fitted with an up/down control.
The welding current can be adjusted from 5 to 160 A and two potentiometers allow respectively the slope down and the post-gas function adjustment. This power source represents the entry level model in the complete range of Cebora DC TIG welding power sources and is mainly intended for maintenance and repair work, as well as for small productions.
The compliance with EN 61000-3-12
brings substantial energy saving and a wide supply voltage tolerance (+15% / -20%).
The power source can be powered by motor generators of adequate power (Min. 6 KVA).
BI-WELDER TIG 2040 DC-HF (Art 265)
BI-WELDER TIG 2040 DC-HF is a single-phase inverter power source
for TIG and MMA-SMAW use, not including AWS6010 cellulosic electrodes, designed for maintenance work and small production batches. The machine may work with pulsed arc, for use on thin workpieces where heat transfer must be minimal and is set up for remote control using the foot control (art. 193), remote control (art. 187), or up-down command on the torch.
The following gases may be used for protection: argon, argon/helium, hydrogen argon.
In TIG mode, the arc is started either in high frequency
or by contact with the Cebora lift
system. It is also possible to save up to 9 welding programs in memory. The compliance with EN 61000-3-12
brings substantial energy saving and a wide supply voltage tolerance (+15% / -20%). The power source can be powered by motor generators of adequate power (Min. 6 KVA).
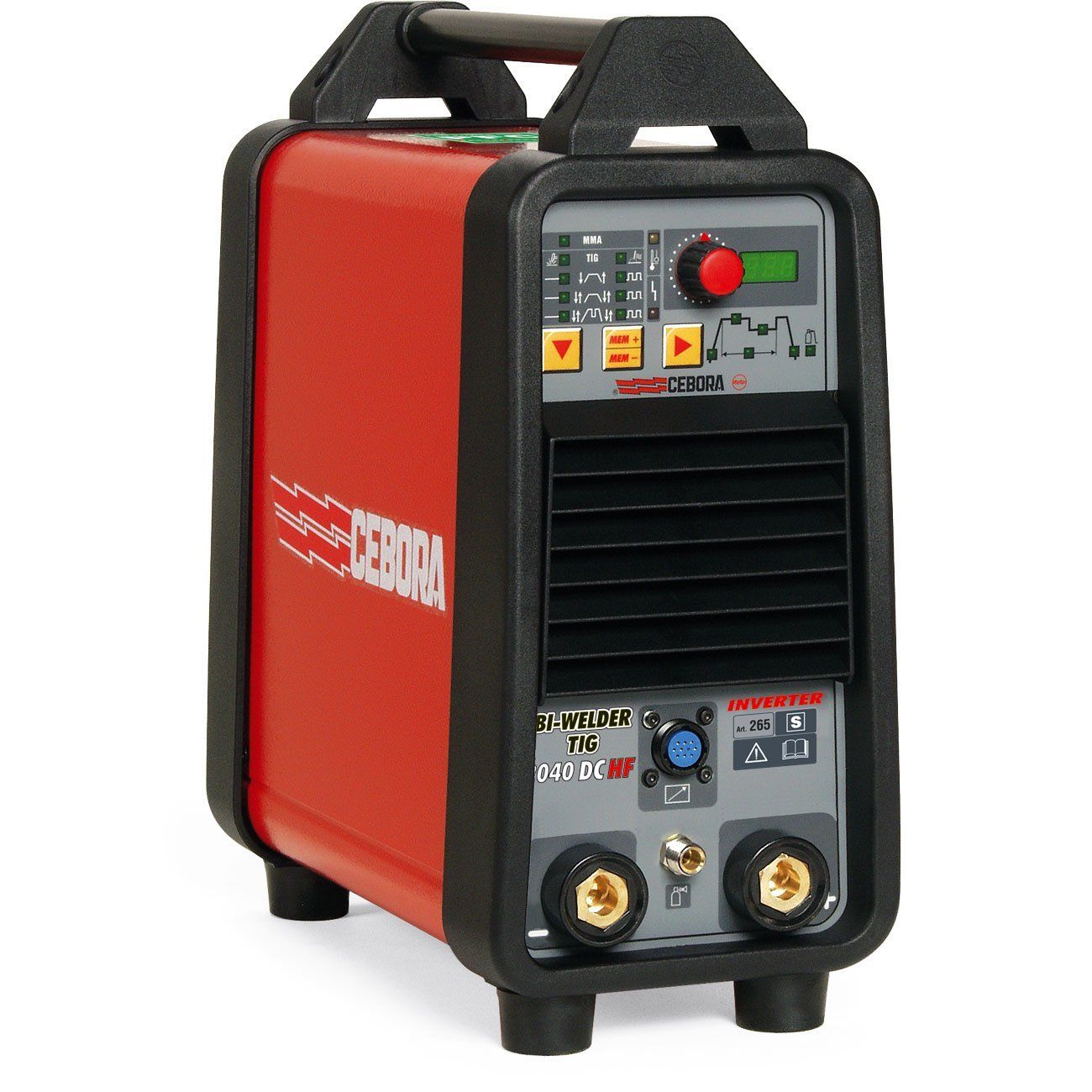
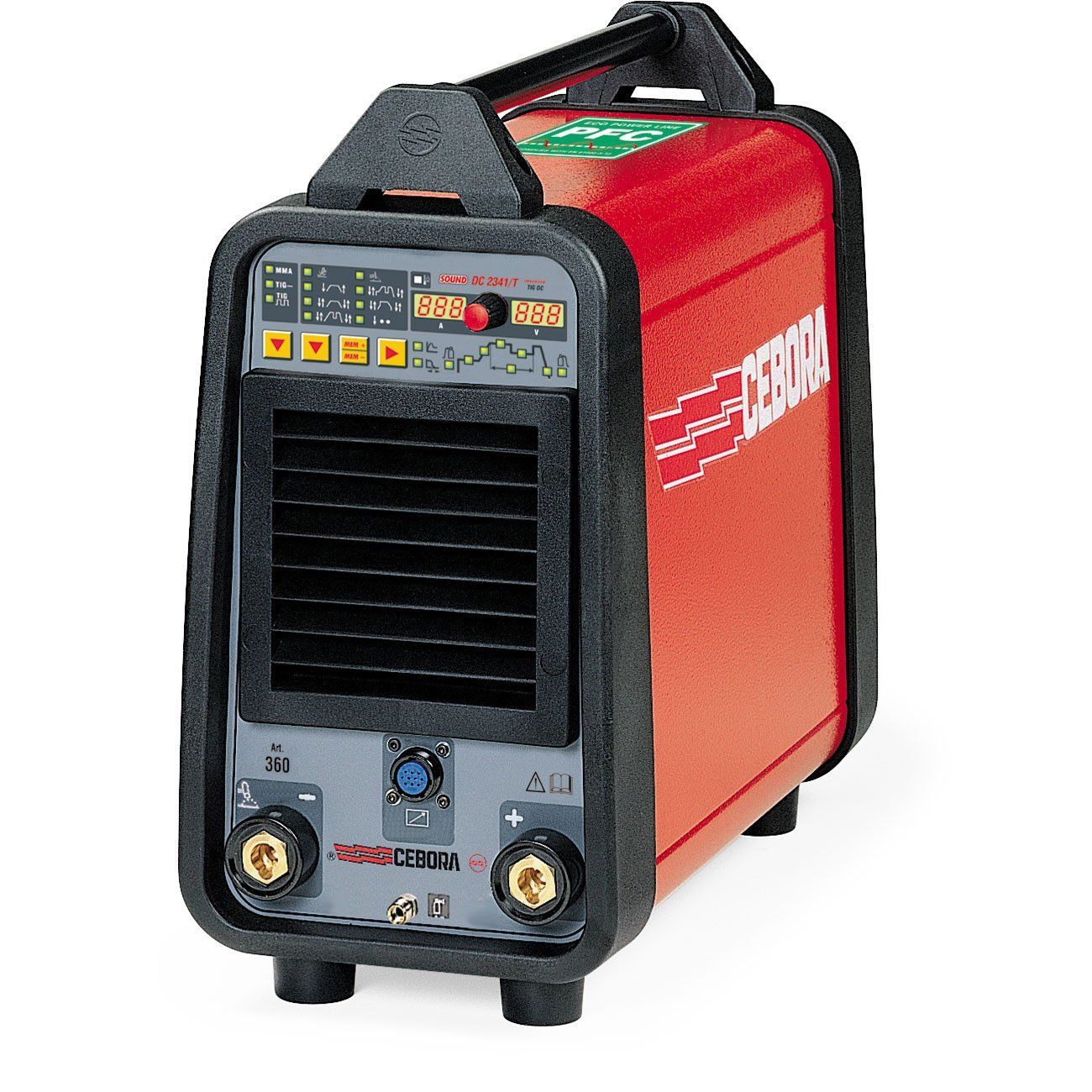
TIG SOUND DC 2341/T (Art 360)
TIG SOUND 2341/T DC is a three-phase (MULTI-VOLTAGE) inverter power source
for TIG and MMA-SMAW use, not including AWS6010 cellulosic electrodes, designed for medium production batches.
The machine may work with pulsed arc, for use also on thin workpieces where heat transfer must be minimal. The machine may be connected to an optional cooling unit (art. 1341) for water-cooled torches. The power source is set up for remote control
via the foot control (art. 193), remote control unit (art. 187) or up-down control on the torch. Its tunnel design allows exceptional cooling efficiency, keeping those components that suffer in dusty environments, such as electronic circuits, out of the cooling flow.
In TIG mode, the arc is started either in high voltage/high frequency or by contact with the Cebora lift system. It is also possible to save up to 9 welding programs
in memory.
Art. 360 is also designed for use with Plasma Welding Console (art. 476.50).
The power source can be powered by motor generators.
Complies with EN 61000-3-12.
TIG SOUND DC 3241/T (Art 362)
TIG SOUND 3241/T DC is a three-phase (MULTI-VOLTAGE) inverter power source
for TIG and MMA-SMAW use, not including AWS6010 cellulosic electrodes, designed for medium production batches. The machine may work with pulsed arc, for use also on thin workpieces where heat transfer must be minimal.
The power source is set up for remote control via the foot control (art. 193), remote control
unit (art. 187) or up-down control on the torch.
Its tunnel design allows exceptional cooling efficiency, keeping those components that suffer in dusty environments, such as electronic circuits, out of the cooling flow. In TIG mode, the arc is started either in high voltage/high frequency or by contact with the Cebora lift system. It is also possible to save up to 9 welding programs
in memory. Art. 362 is also designed for use with Plasma Welding Console (art. 476.50).
Complies with EN 61000-3-12.
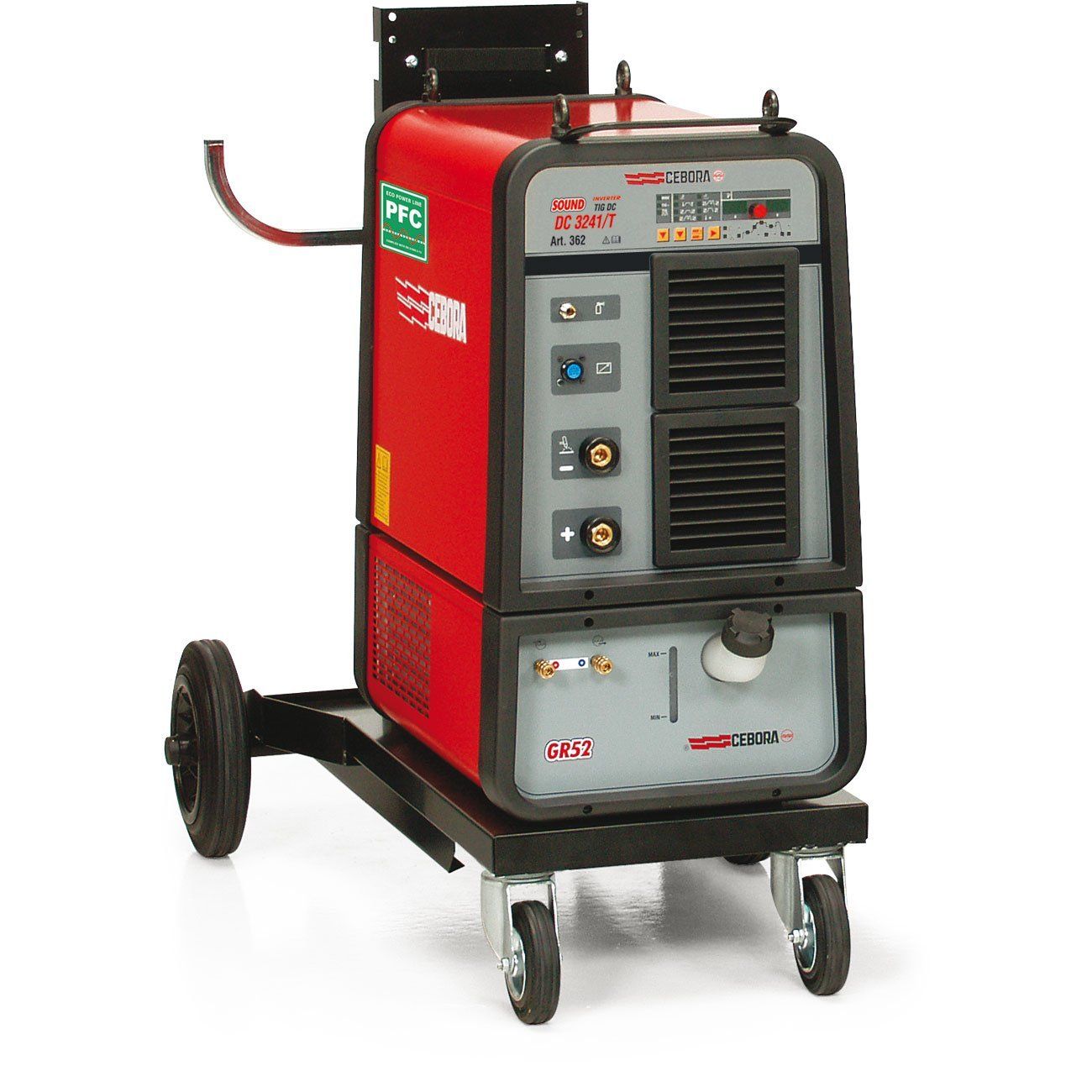
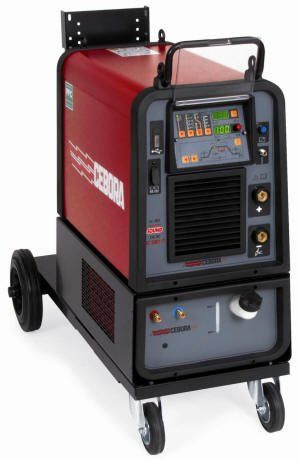
TIG DC EVO 500 T (Art 363)
The TIG DC EVO 500 T, art. 363, is the top of the Cebora DC TIG welding power source range. It is a three-phase power source marked up by a high duty cycle
(500A at 60% and 440A at 100%), suitable for heavy duty use and large production series, also thanks to the built-in cooling unit
manageable from the control panel. It is also capable of welding cellulosic electrodes. Thanks to the PFC system
(which makes the machine comply with the EN61000-3-12 standard), in spite of the great power, the system requires a 32A fuse only.
The new control panel
makes the operator work easier and more user friendly.
The machine may operate with pulsed arc, for intervention even on slim workpieces where transferred heat must be kept to a minimum, as well as in "Spot" mode. The minimum welding current is 5A only. The machine is set up for remote control using the foot control (art. 193), the remote control
(art. 187), or the up-down control on the torch. The tunnel design allows exceptional cooling efficiency, keeping those components that suffer in dusty environments, such as electronic circuits, out of the cooling flow. In TIG mode, the arc is started either in high voltage/high frequency or by contact with the Cebora lift system. It is also possible to save up to nine welding programs.
The machine is equipped with an RS232 port as well as with an USB one for an easy software update.
The power source is also available in a special version suitable for robotic applications as well as for use with Plasma Welding console.
Complies with EN 61000-3-12.
TIG AC-DC INVERTERTIG SOUND AC-DC 1531/M (Art 364)
TIG SOUND AC-DC 1531/M
is a pulsed AC-DC TIG welding power source, inverter technology, featuring HF ignition, as well as a DC MMA welding power source. In TIG mode, the arc is started either in HF or with the Cebora lift system. By means of a first key, you may choose between DC TIG, AC TIG and DC MMA welding mode; a second key allows you to select 2-times / 4-times, pulsed / not pulsed, HF ignition / Lift by Cebora. By means of one encoder you may then control the various adjustments of the power source.
In the AC TIG welding mode, Cebora has implemented an adjustment of the welding parameters which is typical of power sources of higher power.
With the remote control socket it is possible to connect the foot control unit or, alternatively, to work with a torch fitted with Up/Down control.
In DC TIG, the current adjustment is possible between 5 and 150A, while in AC TIG it is possible between 10 and 130A. This power source represents the entry level model in the complete range of Cebora AC-DC TIG welding power sources and is mainly intended for maintenance and repair work, as well as for small productions. The compliance with EN 61000-3-12
brings substantial energy saving and a wide supply voltage tolerance (+15% / -20%). The power source can be powered by motor generators of adequate power (Min. 6 KVA).
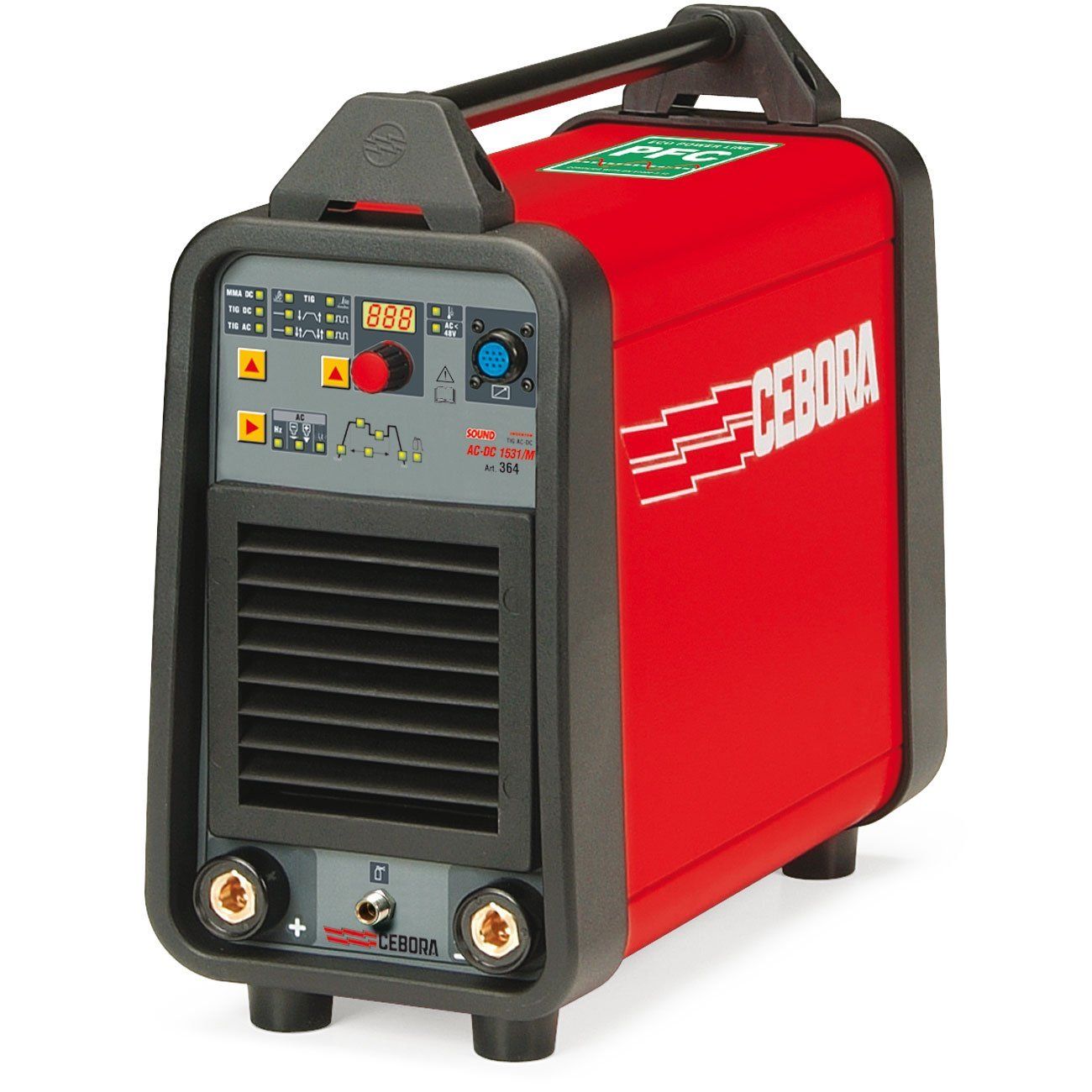
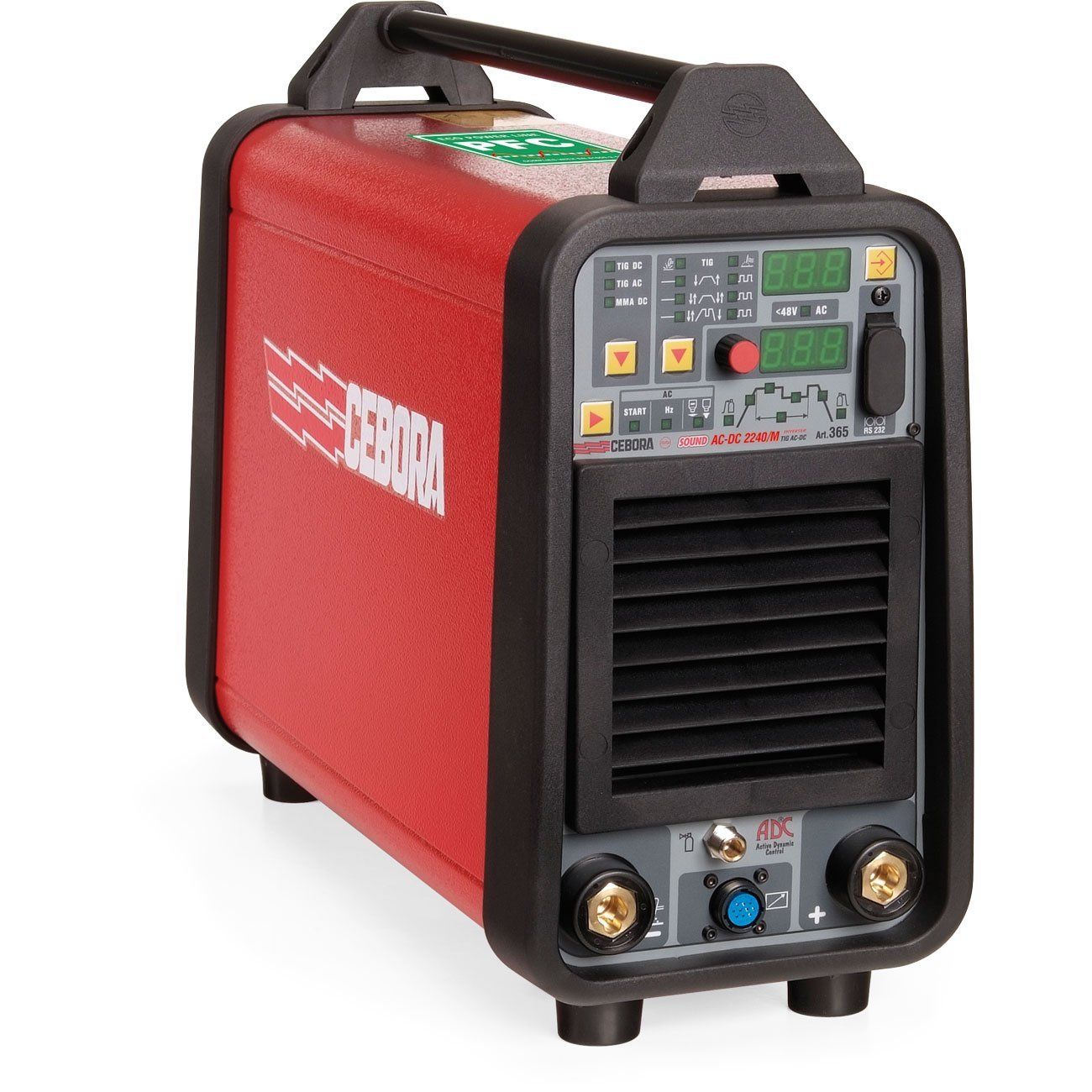
TIG SOUND AC-DC 2240/M (Art 365)
TIG SOUND AC-DC 2240/M
is a single-phase direct and alternating current inverter power source for use in TIG and MMA-SMAW modes (except for cellulosic electrodes). The engineering and manufacturing technology of the machine have produced an excellent duty cycle (220A at 40%, 180A at 60% and 160A at 100%) and a minimum welding current of just 5 Amps. The machine can operate with pulsed arc for working even on thin sheets, where the heat transferred must be kept to a minimum, and may also be connected to an optional cooling unit (art. 1341) for water-cooled torches. There is also an optional (art. 1656) trolley available for moving the power source and cooling unit.
In TIG mode, the arc is started either in high voltage/high frequency or by contact with the Cebora lift system; the machine is also set up for remote control using the foot control (art. 193), remote control (art. 187), or up-down command on the torch. Its tunnel design allows exceptional cooling efficiency, keeping those components that suffer in dusty environments, such as electronic circuits, out of the cooling flow. The adjustable "Hot Start" function enables optimisation of arc ignition in AC.
The PFC system brings substantial energy savings (the machine is suitable also for 16A power supply) and a wide supply voltage tolerance (+15% / -20%). The machine is equipped with a memory for storage of welding programmes and an RS232 port for connection to a computer, enabling easy software updates.
The power source can also be powered by motor-driven generators of adequate power (min. 8 KVA).
Complies with EN61000-3-12.
TIG AC-DC EVO 260 T (Art 369)
The TIG AC-DC EVO 260 T
(Art. 369) is a three-phase inverter power source for use in TIG ACDC, MMA-DC and MMA-AC mode (also for cellulosic electrodes) designed for medium / large production rates. It is an innovative type of power source that allows you to operate in synergic mode: upon selecting the material to be welded, the corresponding thickness and the welding position, the power source sets and suggests the best welding condition. In addition, having in AC the option to choose among nine possible combinations of the three waveforms (square, delta, sine)
allows the operator to customize both the penetration and cleanness of the welding bead.
The new control panel
makes the operator work easier and more user friendly and offers the possibility to regulate directly the main parameters / functions of the welding process. The machine also makes it possible to save up to nine welding programs. The machine may operate with pulsed arc, for intervention even on slim workpieces where transferred heat must be kept to a minimum, as well as in “spot” mode. The minimum welding current is 5A only. The machine is set up for remote control using the foot control (art. 193), remote control (art. 187), or up-down control on the torch. Its tunnel design allows exceptional cooling efficiency, keeping those components that suffer in dusty environments, such as electronic circuits, out of the cooling flow.
In TIG mode, the arc is started either in high voltage / high frequency or by contact with the Cebora lift system. An optional cooling unit
(Art. 1683) is available too. The power source is equipped with an RS 232 port as well as with an USB one for a easy software update.
Complies with EN 61000-3-12.
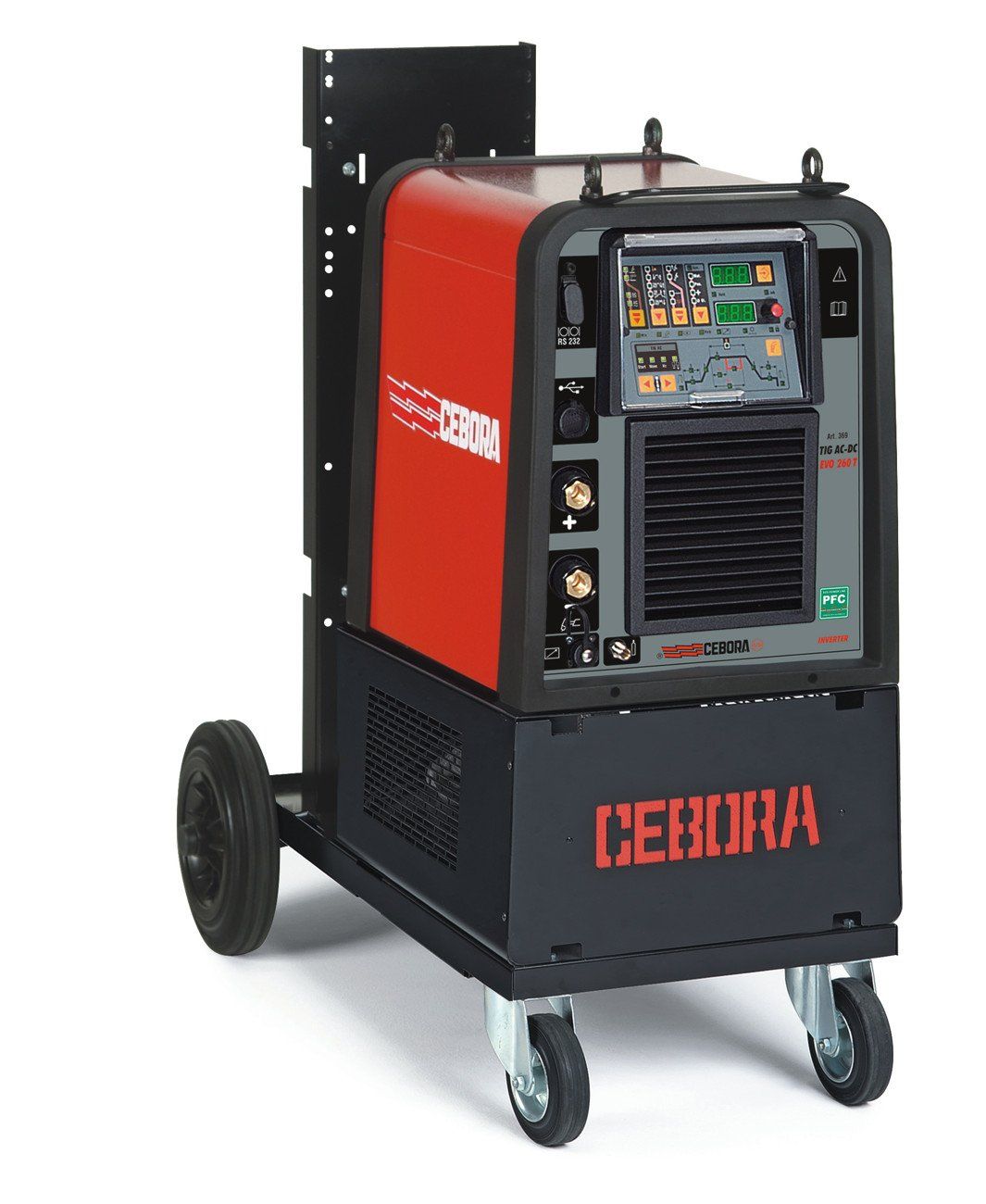
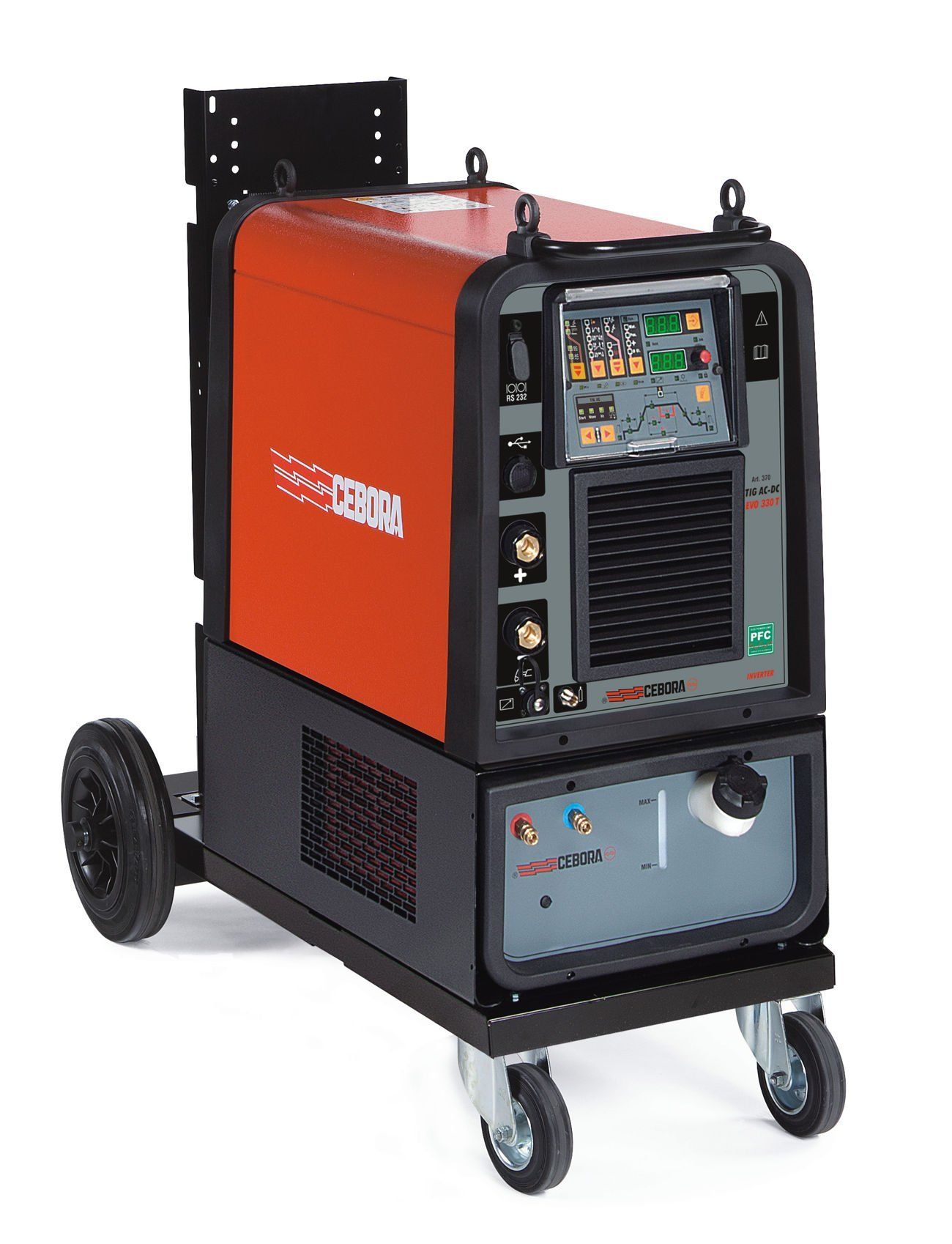
TIG AC-DC EVO 330 T (Art 370)
The TIG AC-DC EVO 330 T
(Art. 370) is a three-phase inverter power source for use in TIG ACDC, MMA-DC and MMA-AC mode (also for cellulosic electrodes) designed for medium / large production rates. It is an innovative type of power source that allows you to operate in synergic mode:
upon selecting the material to be welded, the corresponding thickness and the welding position, the power source sets and suggests the best welding condition. In addition, having in AC the option to choose among nine possible combinations of the three waveforms (square, delta, sine)
allows the operator to customize both the penetration and cleanness of the welding bead.
The new control panel
makes the operator work easier and more user friendly and offers the possibility to regulate directly the main parameters / functions of the welding process. The machine also makes it possible to save up to
nine welding programs. The machine may operate with pulsed arc, for intervention even on slim workpieces where transferred heat must be kept to a minimum, as well as in “spot” mode. The minimum welding current is 5A only. The machine is set up for remote control using the foot control (art. 193), remote control (art. 187), or up-down control on the torch. Its tunnel design allows exceptional cooling efficiency, keeping those components that suffer in dusty environments, such as electronic circuits, out of the cooling flow.
In TIG mode, the arc is started either in high voltage / high frequency or by contact with the Cebora lift system. The power source comes with a built-in cooling unit. The power source is equipped with an RS 232 port as well as with an USB one for a easy software update.
Complies with EN 61000-3-12.
TIG AC-DC EVO 450 T (Art 371)
The TIG AC-DC EVO 450 T
(Art. 371) is a three-phase inverter power source for use in TIG ACDC, MMA-DC and MMA-AC mode (also for cellulosic electrodes) designed for medium / large production rates. It is an innovative type of power source that allows you to operate in synergic mode: upon selecting the material to be welded, the corresponding thickness and the welding position, the power source sets and suggests the best welding condition. In addition, having in AC the option to choose among nine possible combinations of the three waveforms (square, delta, sine)
allows the operator to customize both the penetration and cleanness of the welding bead.
The new control panel
makes the operator work easier and more user friendly and offers the possibility to regulate directly the main parameters / functions of the welding process. The machine also makes it possible to save up to nine welding programs. The machine may operate with pulsed arc, for intervention even on slim workpieces where transferred heat must be kept to a minimum, as well as in “spot” mode. The minimum welding current is 5A only. The machine is set up for remote control using the foot control (art. 193), remote control (art. 187), or up-down control on the torch. Its tunnel design allows exceptional cooling efficiency, keeping those components that suffer in dusty environments, such as electronic circuits, out of the cooling flow.
In TIG mode, the arc is started either in high voltage / high frequency or by contact with the Cebora lift system. The power source comes with a built-in cooling unit. The power source is equipped with an RS 232 port as well as with an USB one for an easy software update.
Complies with EN 61000-3-12.
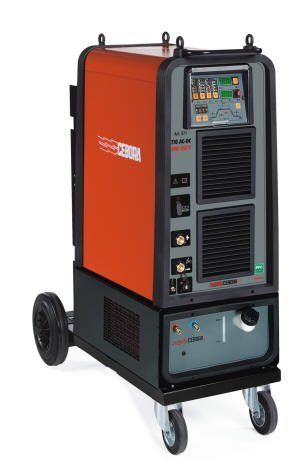
Standard Definition Inverter Plasma Cutters
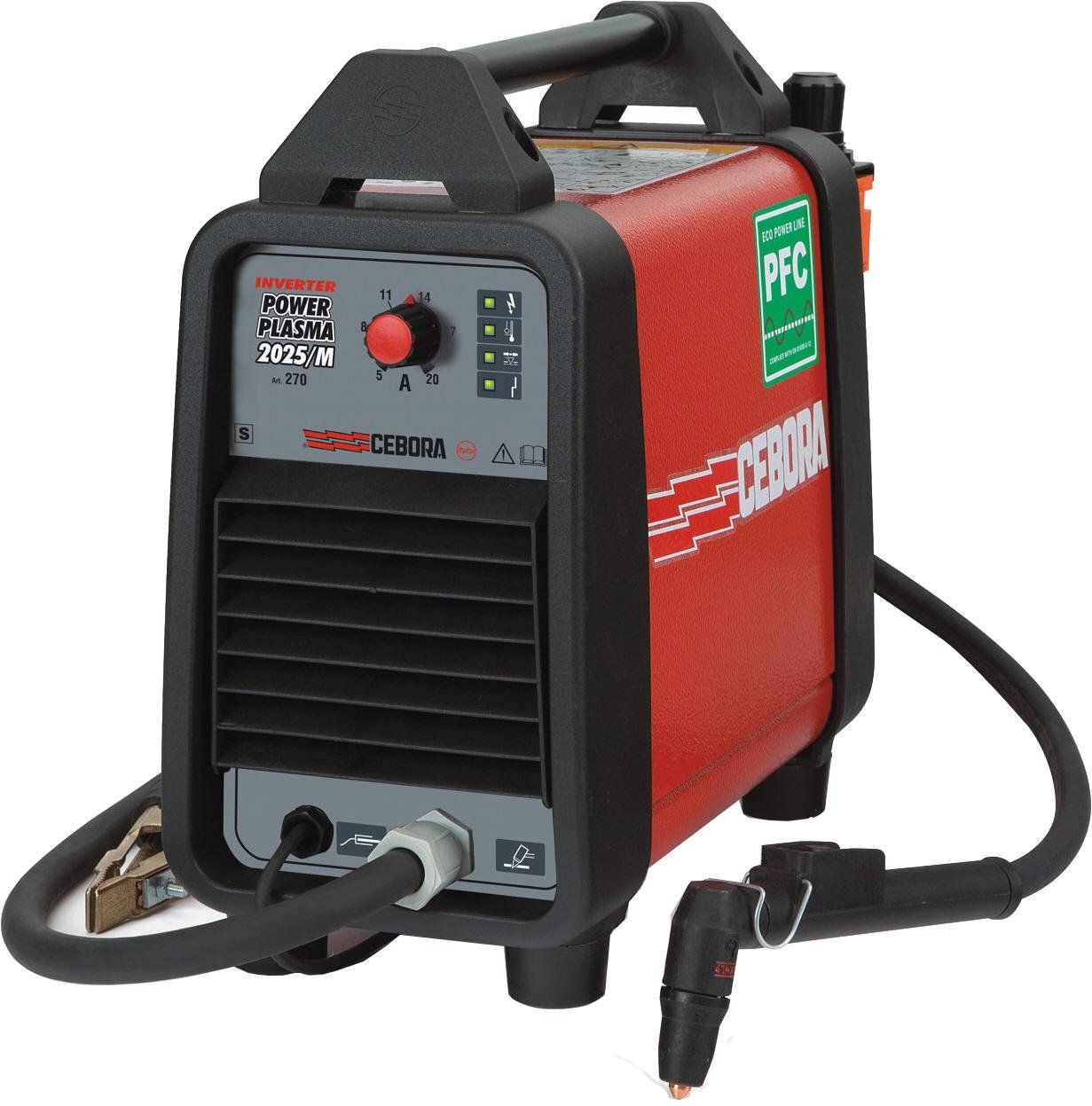
Power Plasma 2025/M - Plasma Inverter (Art 270)
POWER PLASMA 2025/M
was reated to meet the need of working with an easy to handle, easy to use power source with minimal system
requirements (2,3 KVA at the maximum power) yet able to ensure excellent quality cutting on all metals.
POWER PLASMA 2025/M weights just 9,4 kg including the torch, and requires single-phase power supply; it works with compressed air provided at a pressure of 3.5 bar, with an air flow of just 55 l/min (and may thus be powered by a 25-l compressor).
- Pilot arc “on air” operating mode, which makes it possible to work even on painted or coated metals.
- Equipped with a 4 m new Cebora CP41C plasma cutting torch, with “on air” ignition without high frequency.
- High electromagnetic compatibility, per IEC 60974-10, allowing the power source to be used in the vicinity of electronic equipment (such as computers, PLC, etc.).
- Explosion-proof protection of the air reducer unit.
The compliance with EN 61000-3-12
brings substantial energy saving and a wide supply voltage tolerance (+15% / -20%).
The power source can also be powered by motor-driven generators of adequate power (min. 4KVA).
Power Plasma 3035/M Plasma Inverter (Art 279)
POWER PLASMA 3035/M
is an easy to handle, easy to use power source with minimal system requirements, able to ensure excellent quality cutting on all metals, including the new high-strength steels.
POWER PLASMA 3035/M weights just 13 kg including the torch, and requires single-phase power supply; it works with compressed air or nitrogen (for high-quality cutting), provided at a pressure of 3.5 bar, with an air flow of just 60 l/min (and may thus be powered by a 25-l compressor).
The recommended thickness, for the best cutting quality and productivity, is 8 mm; the maximum thickness is 12 mm and the severance thickness is 15 mm.
- Automatic voltage change (115/230 V +15% / -20%).
- Pilot arc operating mode, which makes it possible to work even on painted or coated metals.
- Pilot self-restart, selectable from the panel, to interrupt and automatically reset the arc when cutting screens and grids, increasing operator productivity.
- Nozzle holder protection, as required by standards IEC 60974-7, which eliminates the risk to the operator of direct accidental contact with the gas nozzle.
- High voltage arc striking with high frequency, to ensure reliable lighting of the pilot arc and reduced disturbances.
- High electromagnetic compatibility, per EN50199, allowing the power source to be used in the vicinity of electronic equipment (such as computers, PLC, etc.).
- Explosion-proof protection of the air reducer unit.
The power source is particularly suitable for cutting the overlapped sheets that are commonly used in the car bodies
The compliance with EN 61000-3-12 brings substantial energy saving and a wide supply voltage tolerance (+15% / -20%).
The power source can also be powered by motor-driven generators of adequate power (min. 6KVA).
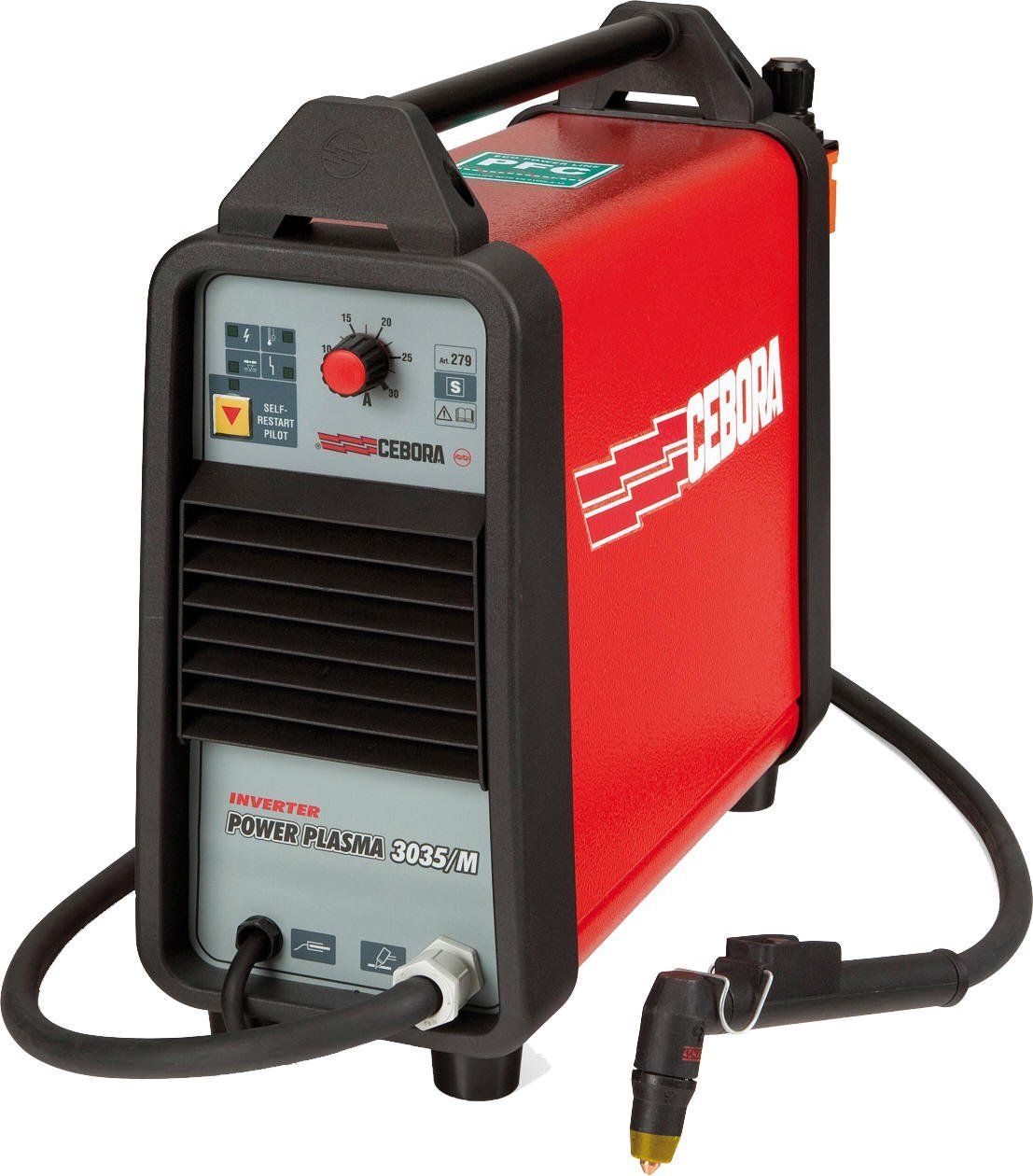
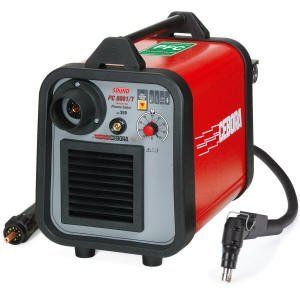
Plasma Sound PC 6061/T (Art. 359)
The POWER PLASMA 6061/T
is a three-phase power source for plasma cutting of metals.
Thanks to the new manual air cooled CP 101 MAR torch,the recommended thickness, for the best cutting quality and productivity, is 20 mm; the maximum thickness is 25 mm and the severance thickness is 30 mm. Its reduced size and weight make the PLASMA SOUND PC 6061/T ideal for on-site work and manual production of medium intensity (60A@60%) and for small automatic production applications, thanks to the cutting speeds and to the high continuous duty cycle (50A@100%).
- Automatic voltage change (208V-220V-230V-400V-440V +/-10%)
- Automatic detection of phase presence (both upon start-up and during operation), to avoid damaging the machine in case the phase is accidentally missing.
- “Post-gas” function which, by cooling the torch after arc shut-off, reduces stress on the components and extends the life-span of consumables.
- Pilot arc operating mode, which makes it possible to work even on painted or coated metals.
- Full-bridge design which allows lower open-circuit voltages.
- Pilot self-restart, selectable from the panel, to interrupt and automatically reset the arc when cutting nets and grids, increasing operator productivity.
- High frequency and high voltage arc striking, which ensures reliable striking of the pilot arc and reduces disturbances.
- High electromagnetic compatibility, per EN50199, allowing the power source to be used in the vicinity of electronic equipment (such as computers, PLC, etc.).
- Central torch adapter with safety protection, to avoid accidental contact with the power parts.
- Explosion-proof protection of the air reducer unit.
- Standard equipped with 6 m CP 101 MAR torch.
Complies with EN 61000-3-12.
The power source can also be powered by motor-driven generators.
Plasma Sound PC 10051/T (Art. 361)
The PLASMA SOUND 10051/T
three-phase power source for plasma cutting of metals represents the upward evolution of the 6061/T.
Thanks to the new manual aircooled CP 161 torch, the recommended thickness, for the best cutting quality and productivity, is 30 mm; the maximum thickness is 35 mm and the severance thickness is 40 mm. The high continuous (85A@100%) and discontinuous (95A@60%) duty cycle and the cutting speed make the PLASMA SOUND PC10051/T ideal for automatic production applications, as well as for manual productions of average size.
- Automatic detection of phase presence (both upon start-up and during operation), to avoid damaging the machine in case the phase is accidentally missing.
- Pilot arc operating mode, which makes it possible to work even on painted or coated metals.
- “Post-gas” function which, by cooling the torch after arc shut-off, reduces stress on the components and extends the life-span of consumables.
- Full-bridge design that allows lower open-circuit voltages
- High electromagnetic compatibility, per EN50199, allowing the power source to be used in the vicinity of electronic equipment (such as computers, PLC, etc).
- High voltage arc striking with high frequency, to ensure reliable lighting of the pilot arc.
- Central torch adapter with safety protection, to avoid accidental contact with the power parts.
- Explosion-proof protection of the air reducer unit.
- “Pilot self-restart” function selectable from the panel, which interrupts and automatically restarts the arc when cutting nets and grids, increasing operator productivity.
- Automatic voltage change between 208/220/230V and between 400/440 V.
- Standard equipped with 6 m CP161 MAR torch
Complies with EN 61000 - 3 - 12
The power source can also be powered by motor-driven generators.
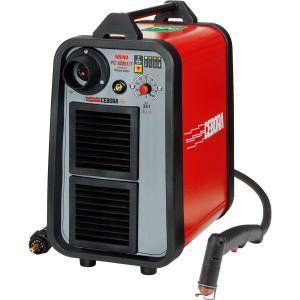
Standard Definition 'Chopper' Plasma Cutters
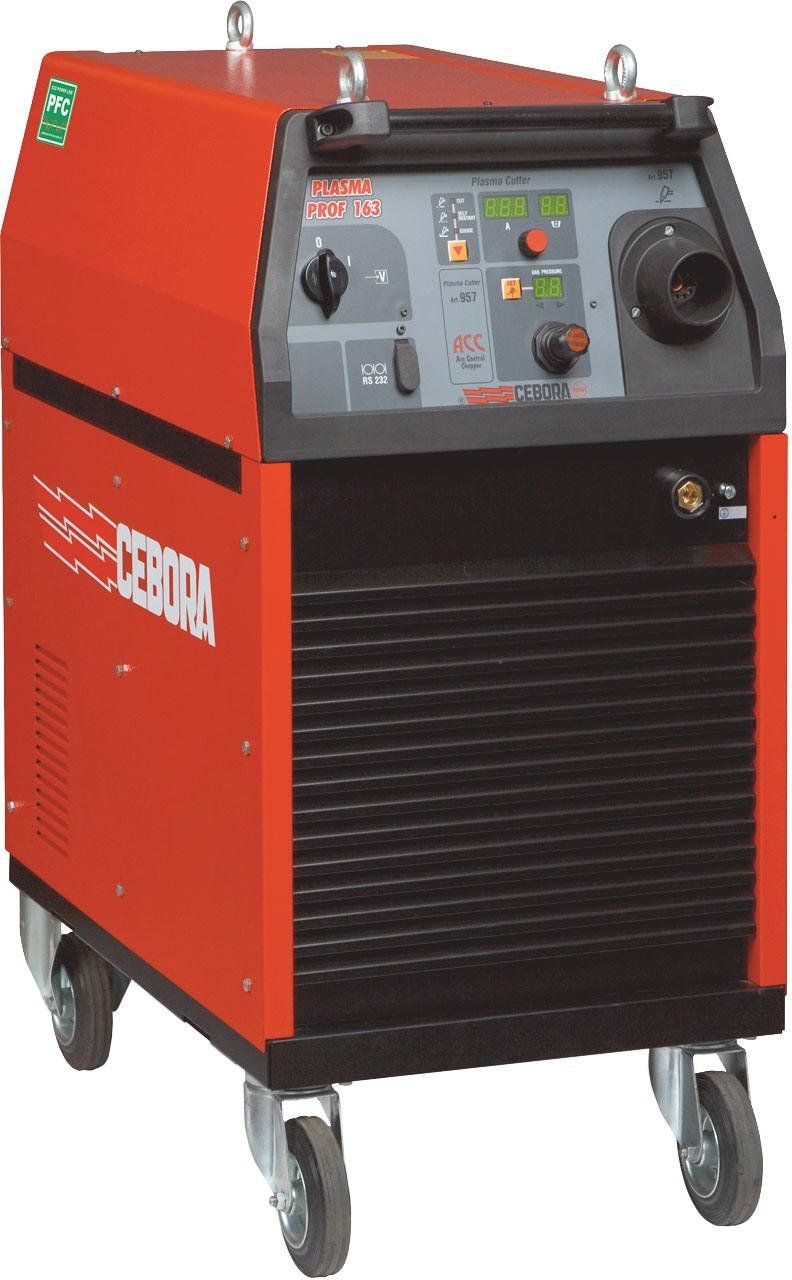
Plasma Prof 163 ACC (Chopper) Art.957
The PLASMA PROF 163 ACC
three-phase “chopper” multi-voltage power source, art. 957, thanks to its remarkable power (160A at 40%) and to the new CP161 torch, assures excellent performances in metal cutting (the recommended thickness, for the best compromise between cutting quality and productivity, is 40 mm; the maximum thickness is 45 mm and the severance thickness is 50 mm. The maximum piercing thickness is 20 mm.
Complies with EN 61000 - 3 - 12
The high continuous (95A at 100%) duty cycle and the cutting speed make the PLASMA PROF 163 ACC ideal for productions of average size.
Main features:
- Continuous monitoring of the supply voltage, detection of abnormal conditions (e.g. missing phase) and safety stop of the power source.
- Air pressure adjustment and test and optimal pressure display, according to the cutting current and to the torch length, on the front panel.
- “Post-gas” function which, by cooling the torch after arc shut-off, reduces stress on the components and extends the life-span of consumables.
- High voltage arc striking with high frequency, to ensure reliable lighting of the pilot arc.
- Reduced electrode-nozzle wear.
- Central torch adapter with safety protection, to avoid accidental contact with the power parts.
- Explosion-proof protection of the air reducer unit.
- Gouging mode that can be selected from the front panel.
- Pilot self-restart function, selectable from the panel, to interrupt and automatically reset the arc when cutting grids.
- Display showing the cutting current and the relevant nozzle diameter to be used.
- RS232 connector on the front panel for updating or customizing the machine software.
- Can be equipped with either 6 or 12 m CP161 torch, for either manual or automated use.
- Ready for use with cutting pantographs by means of analogic interface art. 108 (optional). A remote high frequency unit (art. 481, optional) is also available in order to obtain a maximum total torch cable length of 22 m.
- Automatic recognition of the torch: CP161 MAR / DAR / DAR+HV14.
- Chopper technology and 17 kHz working frequency.
Complies with EN 61000 - 3 - 12
MMA InverterPOWER ROD 131 (Art 256)
The POWER ROD 131 MMA
inverter power source (art. 256) is suitable for MMA welding of all rutile basic electrodes AWS 7018, in stainless steel and aluminium.
The power source is distinguished by a shockproof plastic casing which has made it possible to reduce weight to just 4.5 kg, along with relevant dimensions.
This is a single-phase inverter power source (230V) for MMA and TIG DC welding (with Cebora Lift ignition, using the TIG Cebora T150 torch, art. 1567.01). It can weld electrodes of up to Ø 3.25 and has a duty cycle of 130A at 30% (which becomes 100A at 100%). It is ideal for maintenance and repair works thanks to its lightweight and shockproof plastic casing which makes it suitable for use in many different operating conditions. It features a shoulder strap for easier transport.
The compliance with EN 61000-3-12
brings substantial energy saving and a wide supply voltage tolerance (+15% / -20%).
The power source can be powered by motor generators of adequate power (Min. 6 KVA).
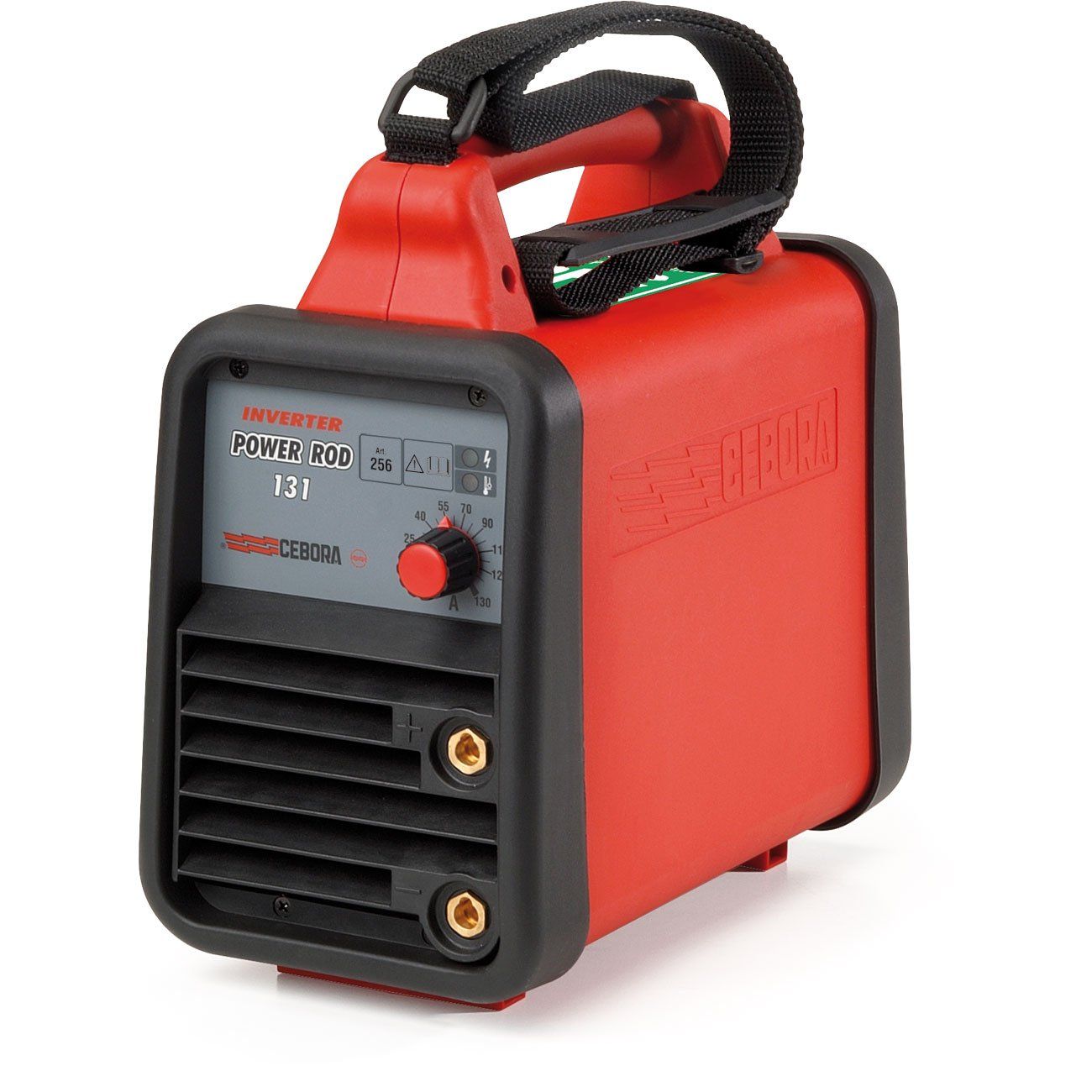
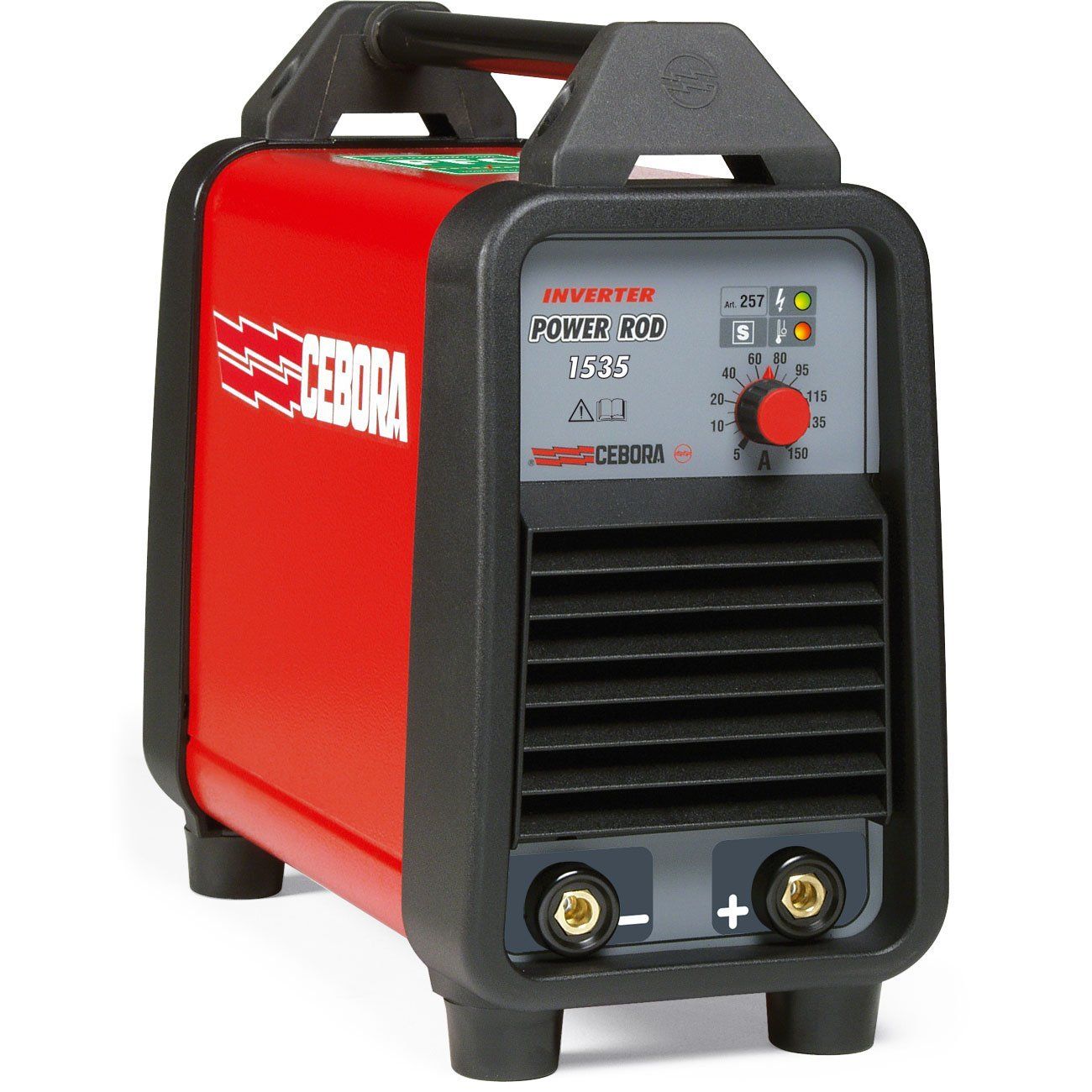
POWER ROD 1535 (Art 257)
The POWER ROD 1535
inverter power source (art. 257) is suitable for MMA welding of all rutile basic electrodes AWS 7018, in stainless steel and aluminium.
It can also be used for TIG DC welding with Cebora Lift ignition, together with the Cebora T150 TIG torch (art. 1567.01).
The thermostatic protection and the high duty cycle 150A at 35% make it suitable for use in even the most extreme conditions.
The power source features devices for protecting the electronic circuits against connection to incorrect power voltage supplies.
The compliance with EN 61000-3-12
brings substantial energy saving and a wide supply voltage tolerance (+15% / -20%).
The power source can be powered by motor generators of adequate power (Min. 6 KVA).
POWER ROD 1840 (Art 261)
The POWER ROD 1840 MMA
inverter power source (art. 261) is suitable for MMA welding of all rutile basic electrodes AWS 7018, in stainless steel and aluminium. It can also be used for TIG DC welding with Cebora Lift ignition.
The high duty cycle (180A at 40%, 150A at 60% and 120A at 100%) makes it suitable for use in even the most extreme conditions. The power source is also equipped with a thermostatic protection.
For MMA welding, a remote control (art. 187) can be connected to the torch control cable connector.
The PFC system assures a substantial energy saving and makes it possible to use the power source with a mains fuse of 16A (slow blow). It also allows to get a wide tolerance on the supply voltage (+15% / -20%).
The IP23 S protection degree makes it possible to use the power source outdoor.
The power source can also be powered by motor-driven generators of adequate power (min. 8KVA).
Complies with EN61000-3-12.
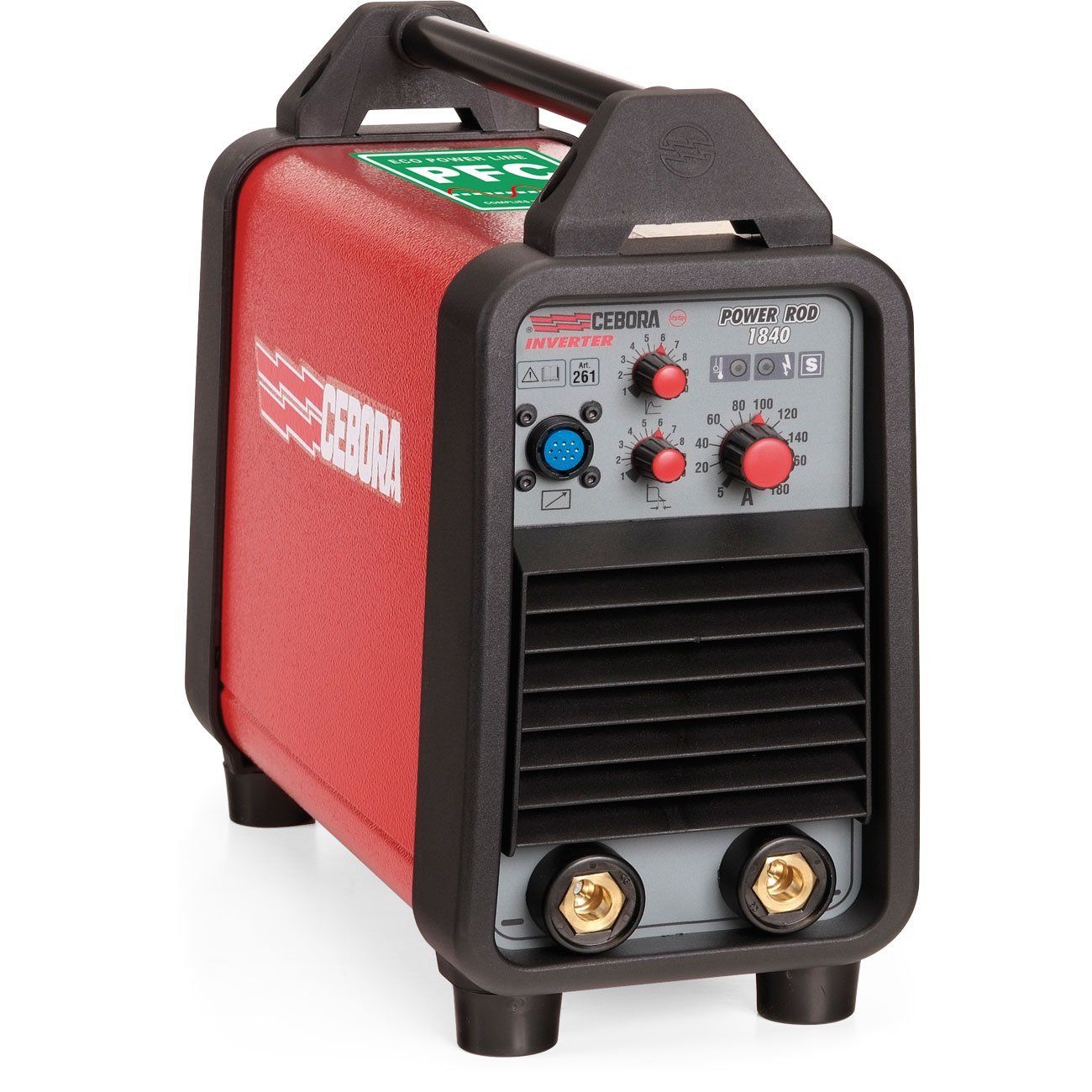
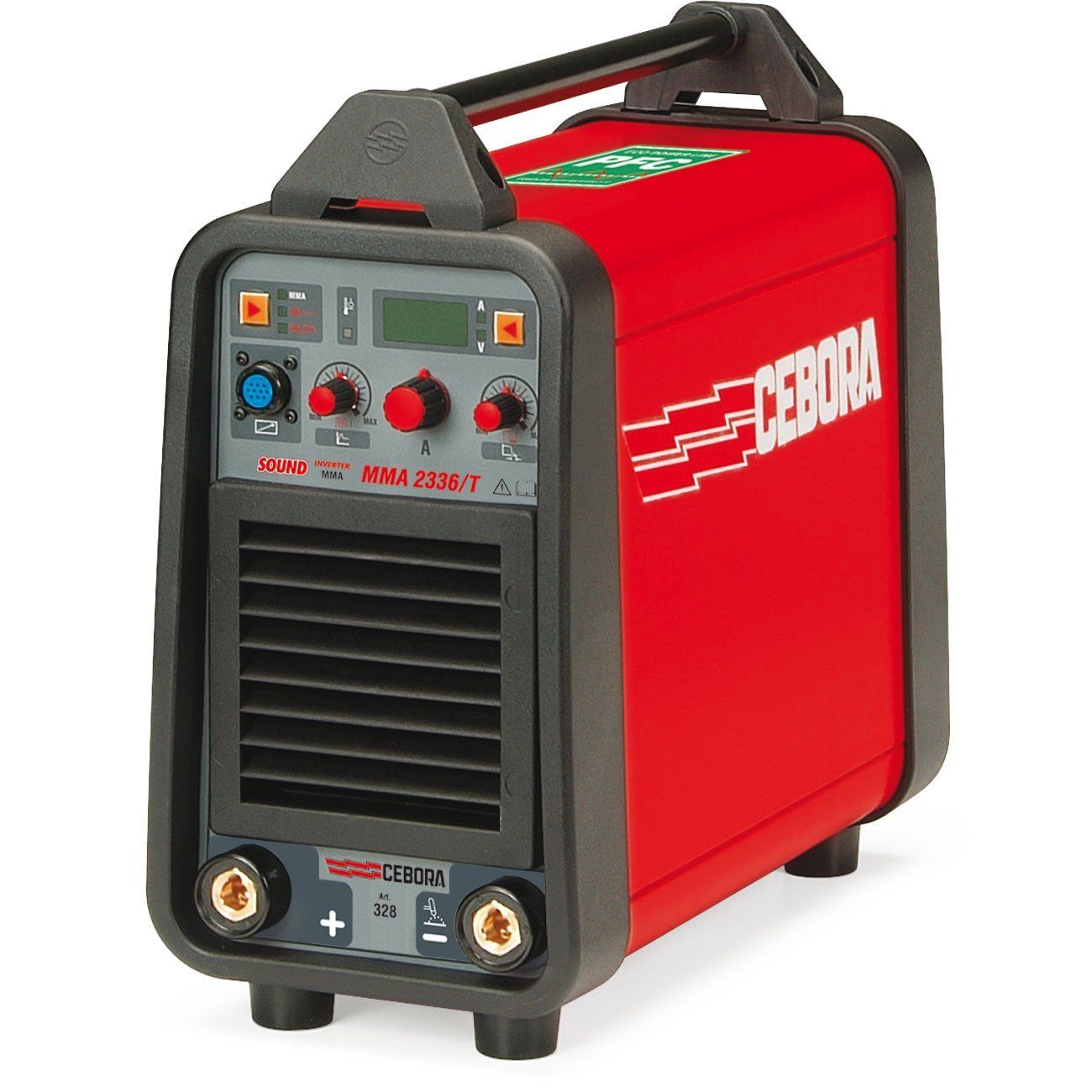
SOUND MMA 2336/T (Art 328)
The three-phase power source SOUND MMA 2336/T
(art. 328) allows professional welding of coated electrodes by means of the Hot Start and Arc Force functions, which assure a sophisticated control of short-circuit conditions, and thus of the electrode transfer, which is the parameter that most strongly affects the welding quality.
The power source is also suitable for D.C. TIG / pulsed TIG welding with "Cebora lift ignition".
The machine program is stored in the flash memory, and may therefore be upgraded.
A connector is included to connect the remote control for the current and digital ammeter to read the welding current.
Complies with EN 61000-3-12.
The power source can be powered by motor generators.
SOUND MMA 3536/T (Art 335)
The three-phase power source SOUND MMA 3536/T
Cell (art. 335) allows professional welding of coated electrodes by means of the Hot Start and Arc Force functions, which assure a sophisticated control of short-circuit conditions, and thus of the electrode transfer, which is the parameter that most strongly affects the welding quality.
It is possible to weld cellulosic electrodes by means of a specialized program available from the panel.
The power source is also suitable for D.C. TIG / pulsed TIG welding with "Cebora lift ignition".
The machine program is stored in the flash memory, and may therefore be upgraded.
A connector is included to connect the remote control for the current and digital ammeter to read the welding current.
Complies with EN 61000-3-12.
The power source can be powered by motor generators.
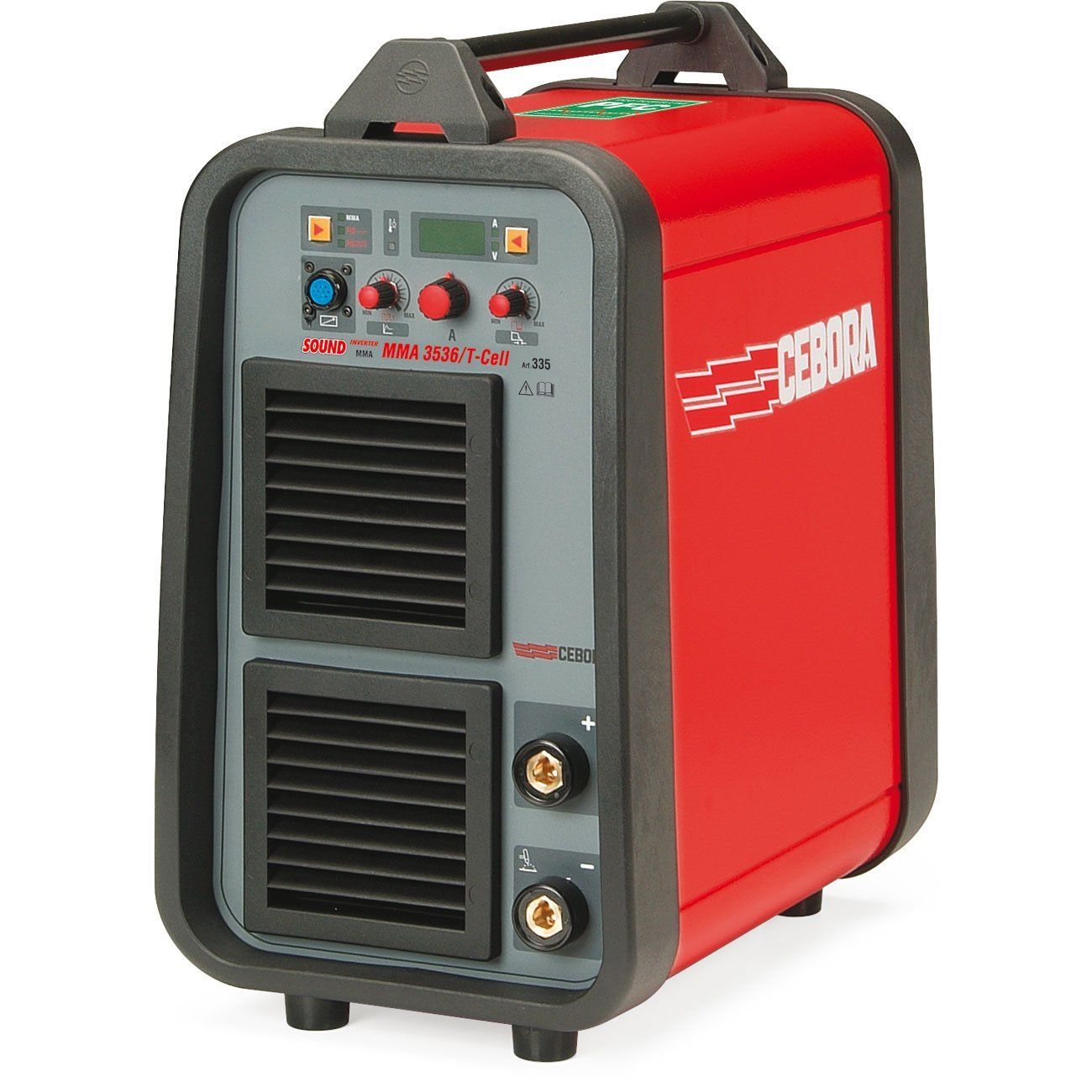
We also manufacture other models and products for:
- MMA Inverters
- MIG-MAG - Compact Evo
- MIG-MAG - Synergic Compact Evo
- Inverter Synergic MIG-MAG
- Inverter Synergic MIG-MAG (with optional pulse)
- Inverter Synergenic Miltiprocess MIG-MAG
- Inverter Synergenic Miltiprocess MIG-MAG (with optional pulse and double pulse)
- Pulsed Inverter Synergic MIG-MAG
- Multiprocess - MIG - TIG - MMA
- Air Cooled Push-Pull Torches
- Spool Gun
- Spotters